OpenAI argues it needs access to ‘avoid forfeiting’ the lead in AI to China.
Category: transportation – Page 3
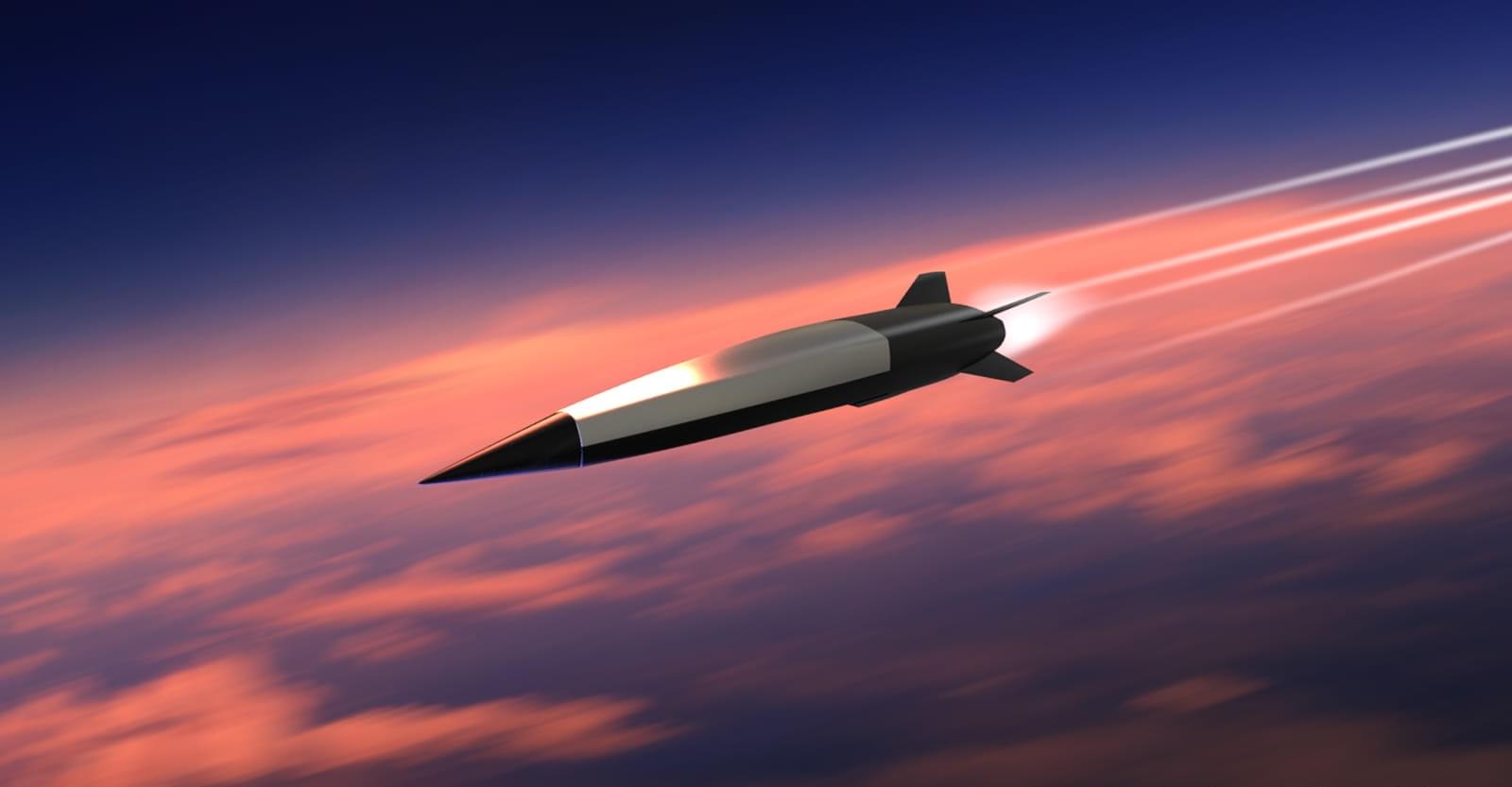
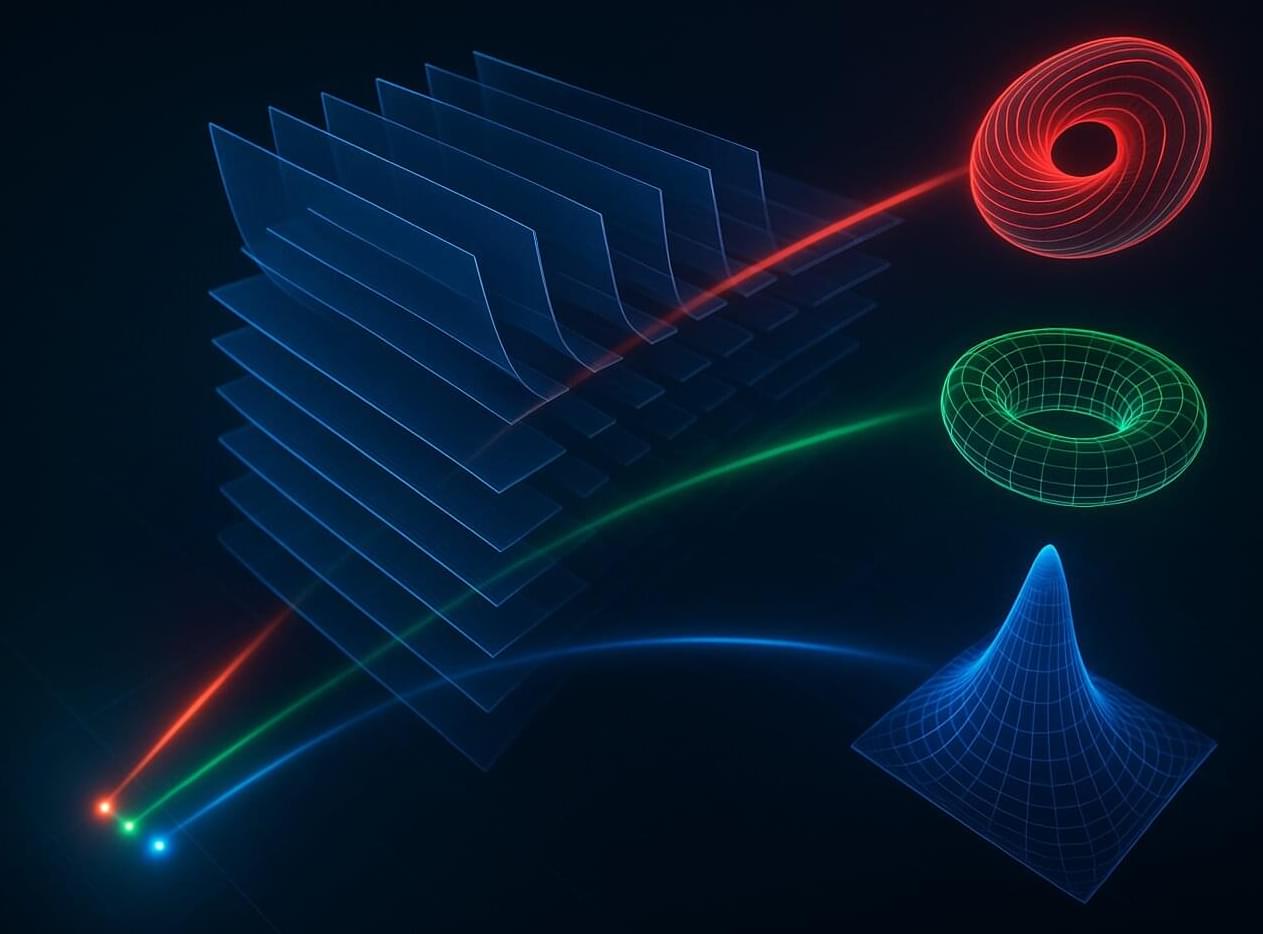
Universal framework enables custom 3D point spread functions for advanced imaging
Engineers at the UCLA Samueli School of Engineering have introduced a universal framework for point spread function (PSF) engineering, enabling the synthesis of arbitrary, spatially varying 3D PSFs using diffractive optical processors. The research is published in the journal Light: Science & Applications.
This framework allows for advanced imaging capabilities—such as snapshot 3D multispectral imaging —without the need for spectral filters, axial scanning, or digital reconstruction.
PSF engineering plays a significant role in modern microscopy, spectroscopy and computational imaging. Conventional techniques typically employ phase masks at the pupil plane, which constrain the complexity and mathematical representation of the achievable PSF structures.
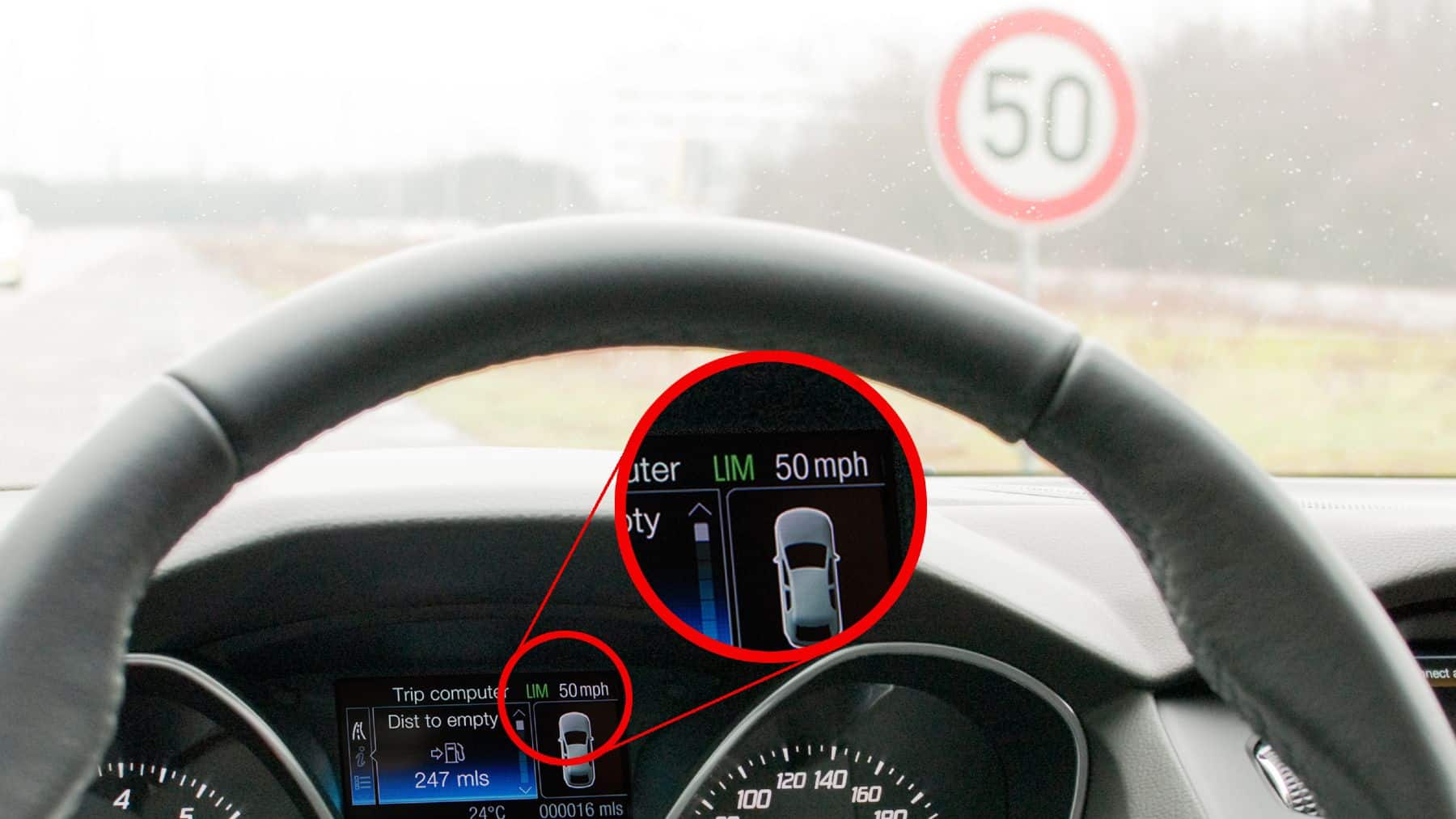

World’s first non-silicon 2D computer developed
Silicon is king in the semiconductor technology that underpins smartphones, computers, electric vehicles and more, but its crown may be slipping, according to a team led by researchers at Penn State.
In a world first, they used two-dimensional (2D) materials, which are only an atom thick and retain their properties at that scale, unlike silicon, to develop a computer capable of simple operations.
The development, published in Nature, represents a major leap toward the realization of thinner, faster and more energy-efficient electronics, the researchers said.
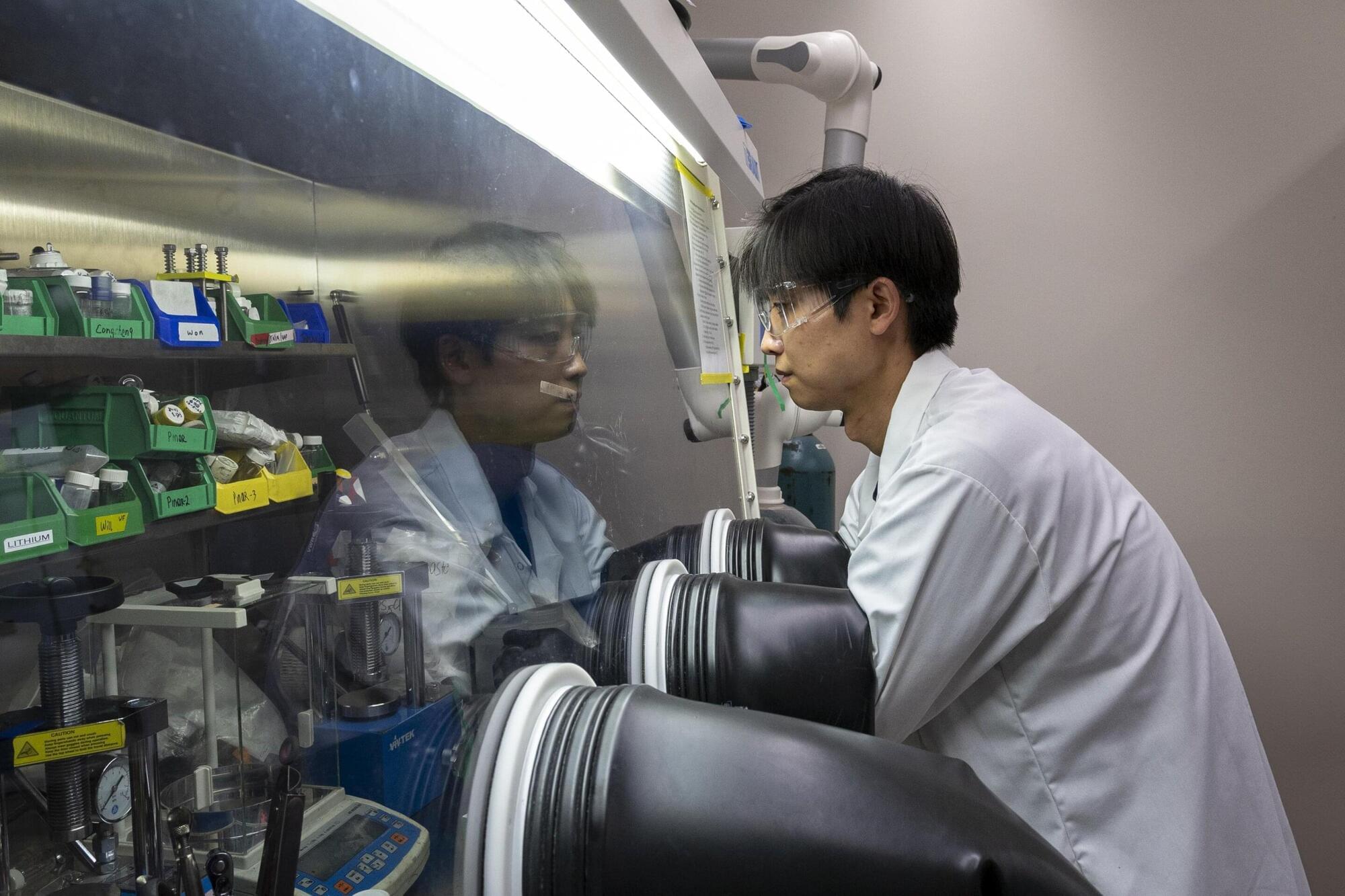
New metal design for solid-state batteries enables operation at lower pressures
Lithium-ion batteries power everything from electric cars to laptops to leaf blowers. Despite their widespread adoption, lithium-ion batteries carry limited amounts of energy, and rare overheating can lead to safety concerns. Consequently, for decades, researchers have sought a more reliable battery.
Solid-state batteries are less flammable and can hold more energy, but they often require intense pressure to function. This requirement has made them difficult to use in applications, but new research from Georgia Tech could change that.
The research group of Matthew McDowell, professor and Carter N. Paden Jr. Distinguished Chair in the George W. Woodruff School of Mechanical Engineering and the School of Materials Science and Engineering, has designed a new metal for solid-state batteries that enables operation at lower pressures. While lithium metal is often used in these batteries, McDowell’s group discovered that combining lithium with softer sodium metal results in improved performance and novel behavior.
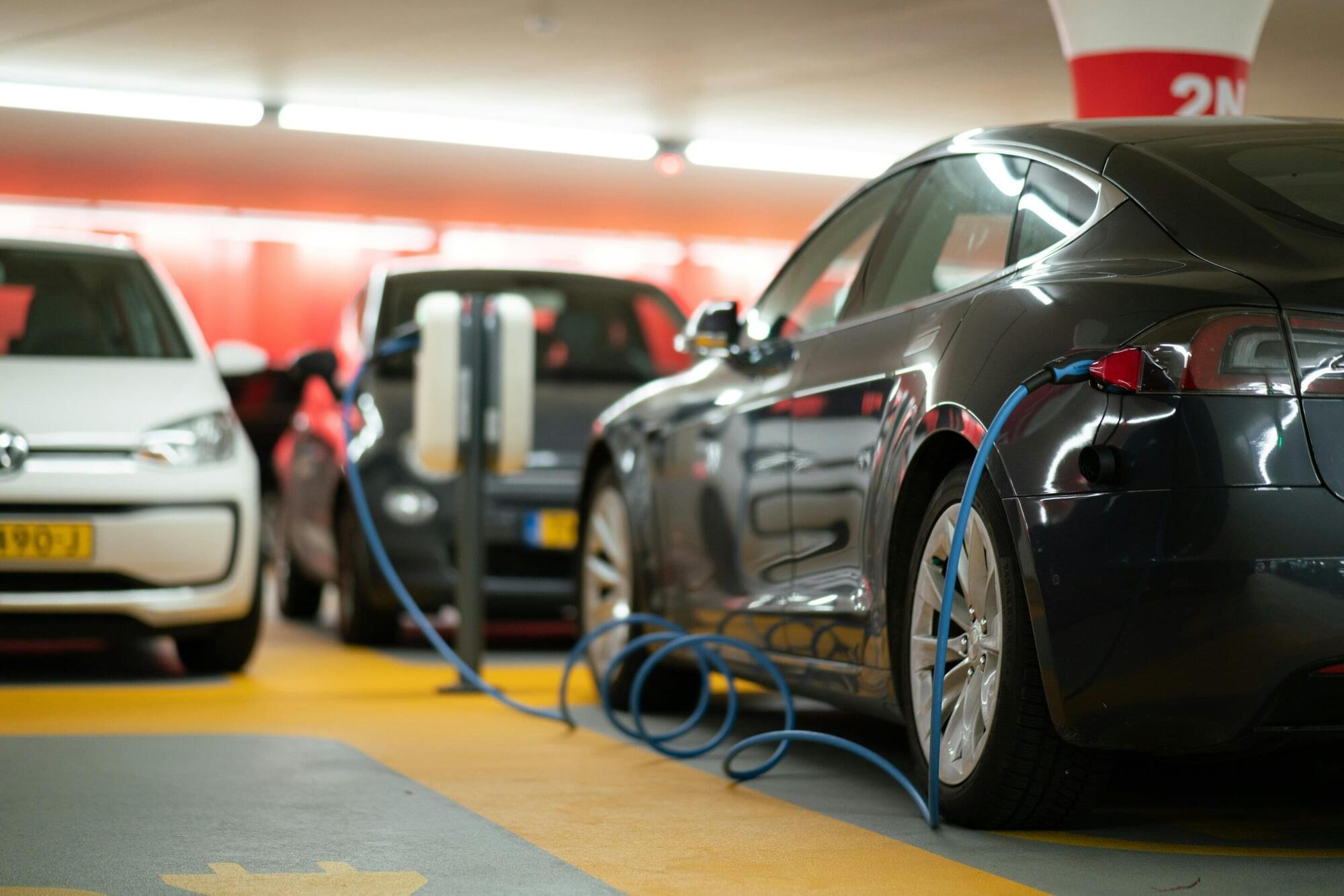
Most people believe misinformation about electric vehicles, international survey finds
More people believe misinformation about electric vehicles (EVs) than disagree with it, according to surveys of four countries, including Australia, Germany, Austria, and the US. The survey found having a conspiracy mentality was the main factor influencing such beliefs, the authors say.
The main misinformation-related concerns for Australians included that EVs are more likely to catch fire, that EVs are intentionally complex to prevent DIY, and that batteries are deliberately non-upgradeable. The authors also found that fact sheets and dialogues with AI-chatbots helped reduce belief in misinformation and increased pro-EV policy support and purchase intentions.
A University of Queensland-led study published in the journal Nature Energy has found misinformation about electric vehicles (EVs) has taken root in society and is primarily fueled by mistrust and conspiracy theories.
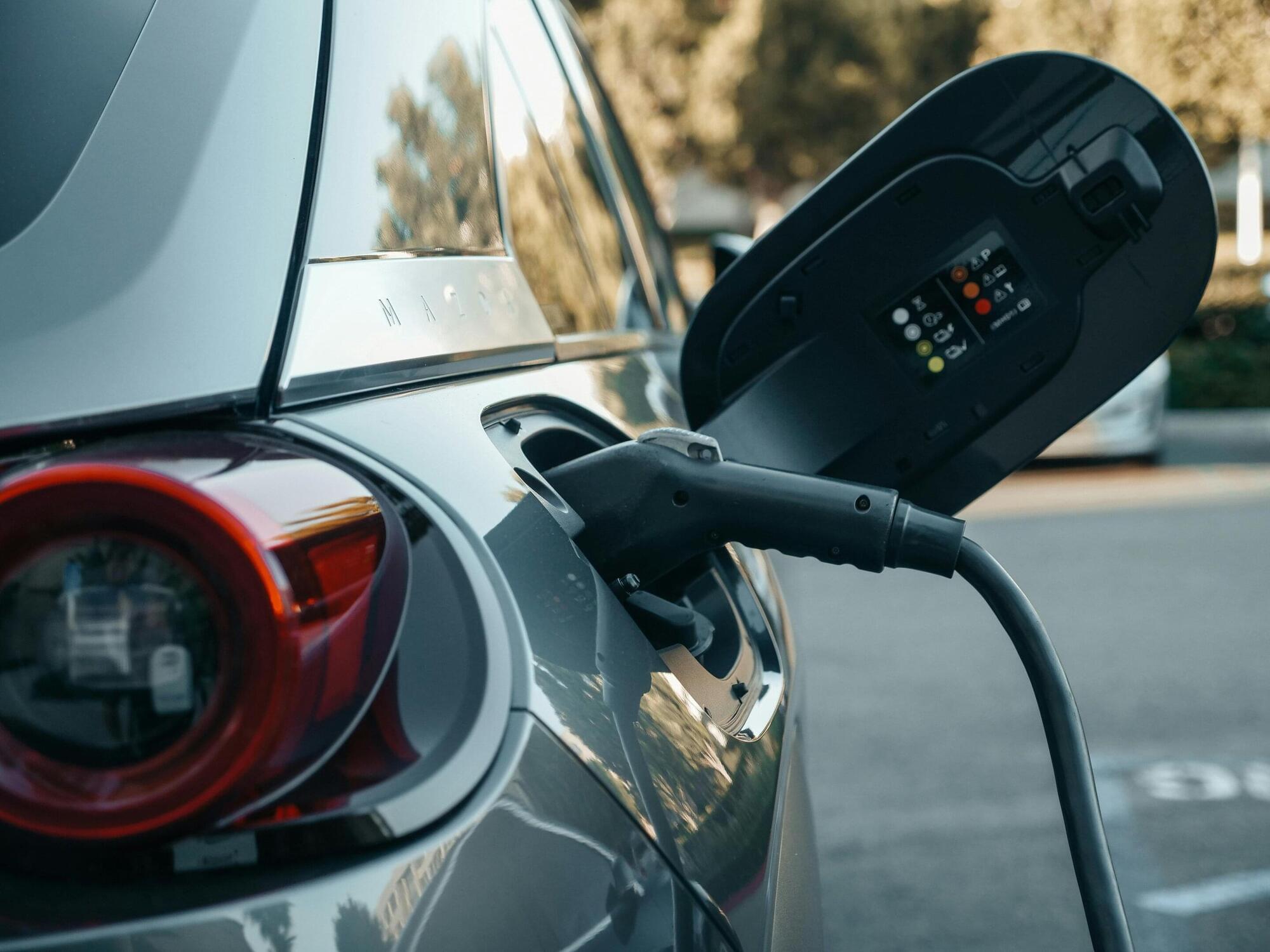
Lithium supply will fall short of growing electric vehicle demand through 2029, analysis finds
In a study published in Cell Reports Sustainability, researchers conducted the most comprehensive analysis to date on lithium supply and demand in China, Europe, and the U.S. Despite the fact that domestic lithium production in some of these regions could grow as much as 10 times by 2030, it would still fall short of the soaring demand for electric vehicles (EVs) without expanding imports or technological innovation.
“Lithium today is as important as gasoline in the industrial revolution,” says author Qifan Xia of East China Normal University in Shanghai. “While lithium reserves are substantial around the world, they are distributed unevenly across different countries. So, we were interested in whether the major EV markets could be self-sufficient.”
Together, China, Europe and the U.S. account for 80% of the world’s EV sales, and their demand is expected to increase further. The team estimated that China might need up to 1.3 million metric tons of lithium carbonate equivalent—a standard measure of lithium content—to produce new EVs. Europe might require 792,000 metric tons, followed by 692,000 metric tons for the U.S.
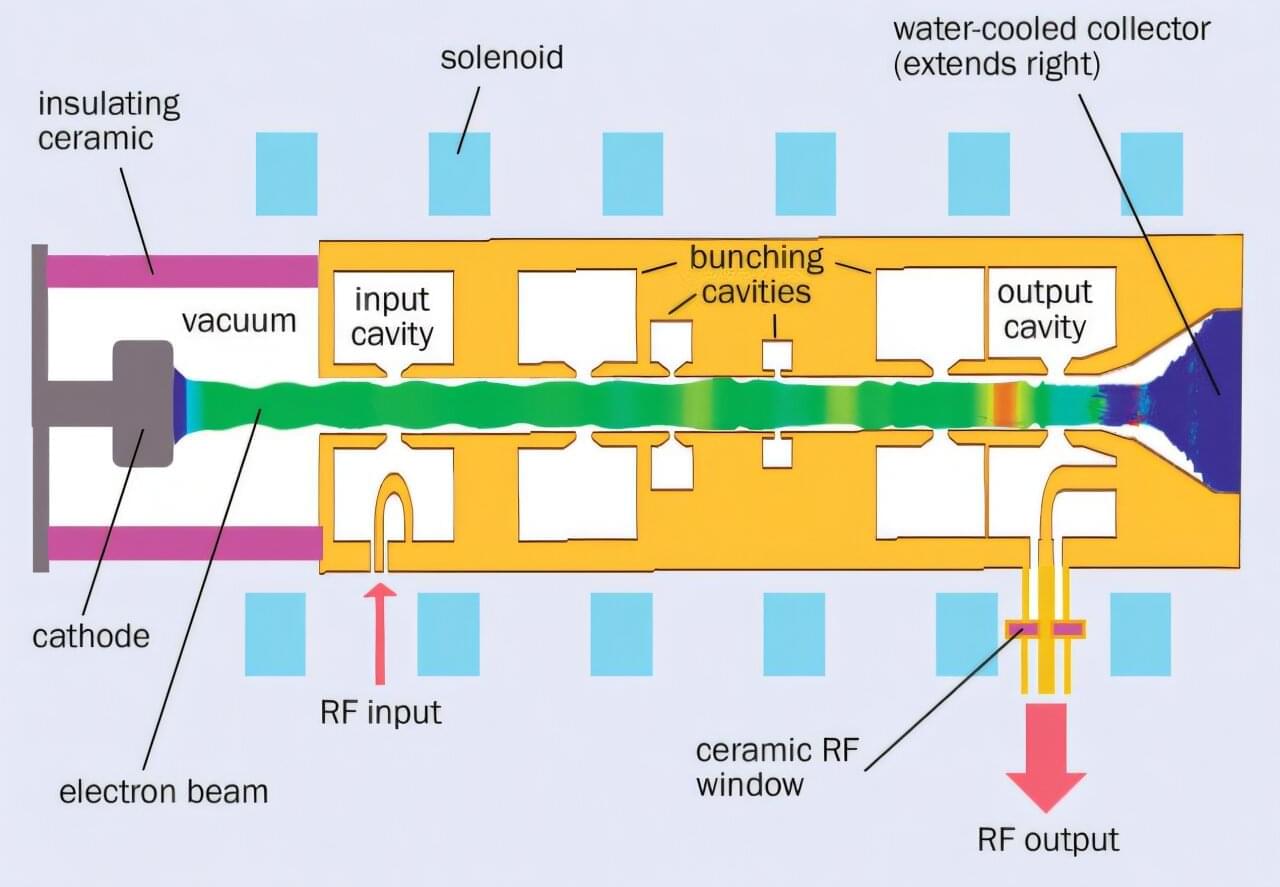
Recent developments in klystron technology for future energy-efficient colliders
The Higgs boson is the most intriguing and unusual object yet discovered by fundamental science. There is no higher experimental priority for particle physics than building an electron–positron collider to produce it copiously and study it precisely.
Given the importance of energy efficiency and cost effectiveness in the current geopolitical context, this gives unique strategic importance to developing a humble technology called the klystron—a technology that will consume the majority of site power at every major electron–positron collider under consideration, but which has historically only achieved 60% energy efficiency.
The klystron was invented in 1937 by two American brothers, Russell and Sigurd Varian. The Varians wanted to improve aircraft radar systems. At the time, there was a growing need for better high-frequency amplification to detect objects at a distance using radar, a critical technology in the lead-up to World War II.
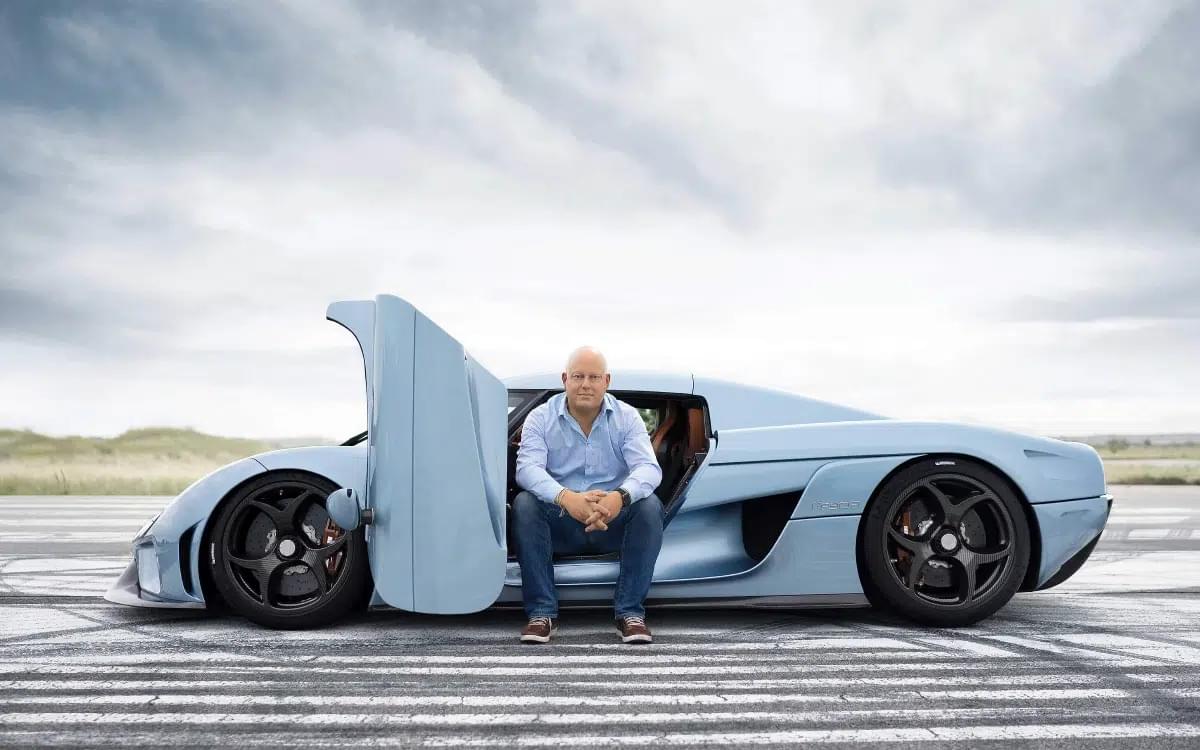