Learn how nuclear licensing is being transformed with AI technology to enhance safety and efficiency in power plants.
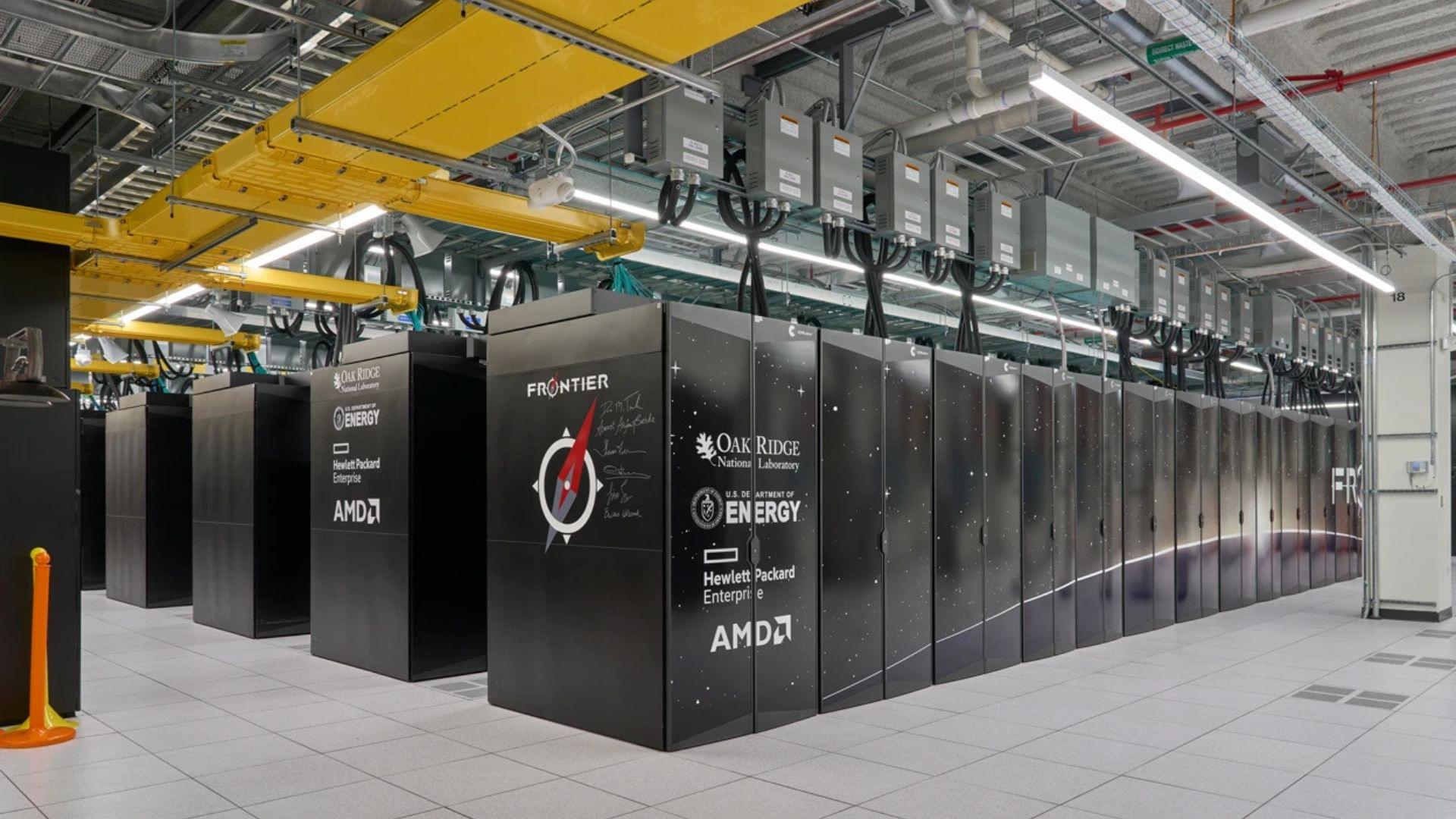
When a 100-year flood hits a city, traffic doesn’t suddenly stop or disappear—it adapts.
“In spite of increasing flood risks, more and more people are moving into flood-prone areas,” said Jianxi Gao, associate professor of computer science at Rensselaer Polytechnic Institute. “This makes it even more urgent to understand how resilient our infrastructure is—and how people adapt when disaster strikes.”
Gao is part of an international team studying how urban transportation systems adapt to extreme weather events like floods. Their work, “Adaptive capacity for multimodal transport network resilience to extreme weather,” published in Nature Sustainability, uses an innovative modeling approach to uncover a universal law governing how travelers shift between private vehicles and public transit during such disruptions. This law reveals that shifts between transport modes, such as from cars to buses, follow predictable patterns driven by changes in travel demand, the density of transport networks, and how modes either compete or support each other.
Air rings blown by dolphins swimming underwater and rings of smoke emitted by jet engines are just two examples of vortex rings. These doughnut-shaped structures and their mesmerizing movement have been studied for decades given their role in propulsion and—in the case of jellyfish and other invertebrates—biological locomotion.
A team of researchers at New York University and NYU Shanghai has uncovered a remarkable property of vortex rings that has been overlooked for more than a century—one that illuminates how these rings respond when they move through water and reach air (i.e., at the water-air interface).
When a vortex ring traveling sideways and up through water reaches the surface and meets air, it can rebound while largely maintaining its shape—much like a tennis ball bouncing off a wall. After the reflection, the ring loses only a small fraction of its energy. However, if the vortex ring moves more directly upward, it breaks apart instead of bouncing.
The Electric Viking
Tesla, led by its innovative and dynamic leadership, is poised for massive growth and has surpassed Apple, which has lost its edge due to poor management and a lack of innovation, in areas such as autonomous vehicles and tech innovation.
Questions to inspire discussion.
Tesla’s Innovation Strategy.
🚀 Q: How does Tesla’s vertical integration contribute to its innovation? A: Tesla’s vertical integration enables it to control the entire product stack, from raw materials to software and service, allowing for tight feedback loops, cost reduction, and rapid iteration in product development.
Tesla is poised to dominate the robotaxi market with its unique, vertically integrated approach and scalable technology, which is expected to disrupt the market, give it pricing power, and potentially drive competitors out ##
## Questions to inspire discussion.
Tesla’s Robotaxi Strategy.
🚗 Q: How is Tesla accelerating its robotaxi rollout? A: Tesla is expanding geography in Austin, offering safe and fully autonomous Waymo rides on Uber, and entering the Indian market, with Wall Street underestimating the potential of these incremental moves.
🏭 Q: What advantages does Tesla have in the robotaxi market? A: Tesla’s vertically integrated technology allows them to control their destiny and cost structure from silicon to cleaning head, giving them a significant edge over competitors relying on partnerships and procurement.
Market Impact and Competition.
Many essential products, from smartphones and magnets to electric vehicles, semiconductors and wind turbines, need rare earth metals to perform.
The rapidly growing demand for these critical products has led to increased need for domestic production of rare earth elements (REEs). However, according to the U.S. Geological Survey, the nation is still lagging globally behind countries such as China, with just over 14% of the world’s REE raw ore production and none of the world’s refining capacity. Purdue University is changing this harsh reality by using its patented rare earth technology in a partnership with Indiana-based ReElement Technologies in an effort to narrow the gap between the U.S. and the rest of the world in this critical industry.
Indy-area company builds on cutting-edge Purdue technology to help narrow the international gap in essential area.
Tesla’s robo-taxi service has the potential to lead to a trillion-dollar valuation due to its scalable, low-cost AI approach, and could generate trillions of dollars in profit, significantly outpacing competitors.
Questions to inspire discussion.
Tesla’s Robo Taxi Business Model.
🚗 Q: What potential profit could Tesla’s robo taxi model generate per vehicle? A: Tesla’s robo taxi model could generate $150,000 in profit per year from each vehicle if charging prices similar to Uber.
Questions to inspire discussion.
🤝 Q: What are the potential issues with the Uber-Lucid-Neuro robotaxi partnership? A: The partnership is a “cluster f waiting to happen” due to independent entities involved, which typically end in a “messy divorce”, making it potentially uncompetitive against fully integrated solutions like Tesla’s.
🗺️ Q: How does Tesla’s robotaxi service area expansion compare to Waymo’s? A: Tesla expanded its service area in 22 days, while Waymo’s first service area expansion in Austin, Texas took 4 months and 13 days, demonstrating Tesla’s faster and more aggressive approach to expansion.
Business Viability.
💼 Q: What concerns exist about the Uber-Lucid-Neuro robotaxi partnership’s business case? A: While considered a “breakout moment” for autonomous vehicles, the business case and return on investment for the service remain unclear, according to former Ford CEO Mark Fields.
🏭 Q: What manufacturing advantage does Tesla have in the robotaxi market? A: Tesla’s fully vertically integrated approach and ability to mass-manufacture Cyber Cabs at a scale of tens of thousands per month gives it a significant cost-per-mile advantage over competitors using more expensive, non-specialized vehicles. ## Key Insights.