The innovation by researchers at the GC’s Advanced Science Research Center could enable development of a range of flexible, impenetrable materials capable of protecting the body and fragile objects.
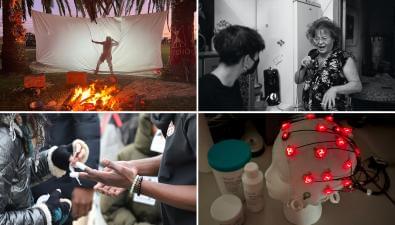
A groundbreaking cement developed by Chinese scientists can now generate electricity from heat—thanks to a bio-inspired design that mimics plant stems. By combining hydrogel layers with traditional cement, this innovation enhances ion flow and delivers record-high thermoelectric efficiency. This breakthrough could power smart infrastructure, allowing buildings, roads, and bridges to self-generate electricity for sensors, lighting, and more—ushering in a new era of energy-smart cities.
A research team has succeeded in inducing ferromagnetism, a key property of conventional magnets, in pure vanadium oxide, a compound not previously recognized for such magnetic behavior. Through a series of experiments, the team verified that by precisely adjusting the oxidation state of vanadium ions, they could induce the element to behave magnetically.
The research is published in the journal Advanced Functional Materials. The team was led by Professor Chun-Yeol You from the Department of Physics and Chemistry at DGIST.
Vanadium oxide (VO) is widely known for its metal-insulator transition (MIT), a phenomenon in which its electrical conductivity dramatically changes depending on temperature. While its electronic properties have been extensively studied, its magnetic properties —especially the possibility of ferromagnetism—remain largely unexplored. VO typically exhibits antiferromagnetic or paramagnetic behavior, which limits its application as a magnetic material.
Tiny pieces of plastic are an increasingly big problem. Known as microplastics, they originate from clothing, kitchen utensils, personal care products, and countless other everyday objects. Their durability makes them persistent in the environment – including in human bodies.
Not only are many people on Earth already contaminated by microplastics, but we’re also still being exposed every day, as there is minimal regulation of these insidious specks.
According to a new literature review, a significant portion of our microplastic exposure may come from drinking water, as wastewater treatment plants are still not effectively removing microplastics.
Bio-batteries constructed by electroactive microorganisms have unique advantages in physiological monitoring, tissue integration, and powering implantable devices due to their superior adaptability and biocompatibility. However, the development of miniaturized and portable bio-batteries that are plug and play and compatible with existing devices remains a challenge.
In a study published in Advanced Materials, a team led by Zhong Chao, Liu Zhiyuan, and Wang Xinyu from the Shenzhen Institutes of Advanced Technology of the Chinese Academy of Sciences, collaborating with Wang Renheng from the Shenzhen University, developed a miniaturized, portable bio-battery that enables precise control over bioelectrical stimulation and physiological blood pressure signals.
The researchers encapsulated Shewanella oneidensis MR-1 biofilms within alginate hydrogels to develop living hydrogels, which can be 3D printed into defined geometries for customized fabrication. Inspired by lithium-ion battery fabrication, they developed a miniaturized bio-battery (20 mm in diameter, 3.2 mm in height) using living hydrogel as the bio-anode ink, K3[Fe(CN)6]-containing alginate hydrogel as the cathode ink, and a Nafion membrane as the ion exchange membrane.
Recently, a group of researchers discovered a novel way to achieve spin-valve effects using kagome quantum magnets.
“This approach uses a prototype device made from the kagome magnet TmMn₆Sn₆,” explained Associate Prof. XU Xitong, “This breakthrough eliminates the need for the complex fabrication techniques traditionally required by spin-valve structures.”
The findings were published in Nature Communications. The team was led by Prof. Qu Zhe from the Hefei Institutes of Physical Science of the Chinese Academy of Sciences, together with Prof. Chang Tay-Rong from National Cheng Kung University.
Although lumber does show promise as a renewable alternative to structural materials such as steel and concrete, it still tends to be a bit weaker than those substances. Scientists have now set about addressing that shortcoming, by strengthening wood with added iron.
Led by Asst. Prof. Vivian Merk, a team of researchers at Florida Atlantic University (FAU) started out with cubes of untreated red oak hardwood. Red oak – along with hardwoods like maple, cherry and walnut – is an example of what’s known as ring-porous wood. In a nutshell, this means that it utilizes large ring-shaped internal vessels to draw water up from the tree’s roots to its leaves.
The scientists proceeded to mix ferric nitrate with potassium hydroxide, creating a hard iron oxide mineral called nanocrystalline ferrihydrite, which occurs naturally in soil and water. Utilizing a vacuum impregnation process, nanoparticles of that ferrihydrite were drawn into the wood and deposited inside of its individual cell walls.
UCLA researchers have developed a groundbreaking graphene-protected catalyst that extends hydrogen fuel cell lifespans beyond 200,000 hours.