Objects can now be 3D-printed in opaque resin.
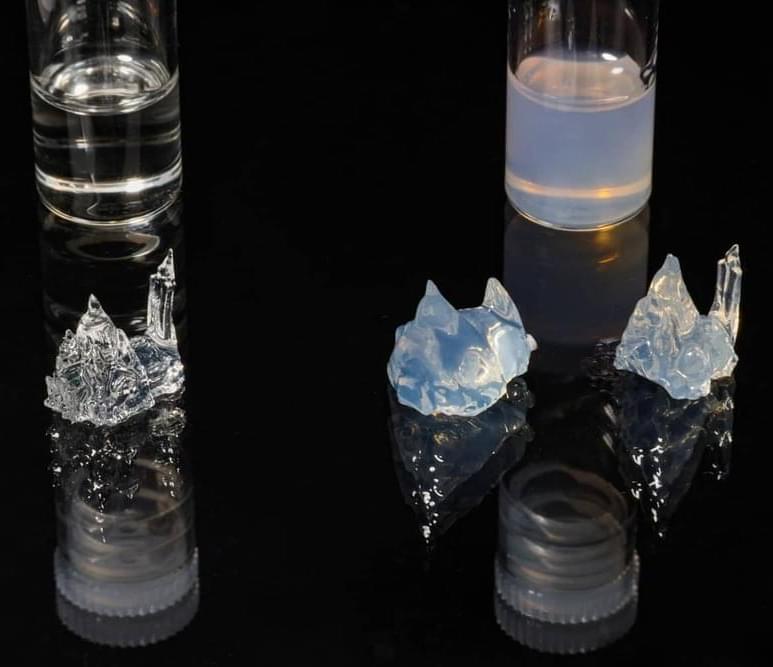
Admatec has steadily been increasing its 3D printing capabilities, taking its slurry-based digital light processing (DLP) process further. First it expanded from resins loaded with ceramic particles to those loaded with metal particles. It then increased the build volume of its Admaflex300 3D printer. Now, the company has introduced a new integrated debinding and sintering furnace with a larger work volume.
The majority of ceramic 3D printing processes rely on the use of a photopolymer slurry loaded with ceramic particles. Once printed, these green parts first go through a debinding process, in which the photopolymer material is removed, followed by sintering, causing the part to become fully dense.
Circa 2020
Researchers have created a new 3D printing technique that could replace traditional 3D printers that take far to long to create desired objects.
The problem with traditional 3D printers is that they work in horizontal layers. This process is the bane of 3D printing, as it means that, depending on the size of the object, it will take time to construct. What if the printer could build the entire model all at once, instead of layer-by-layer? Researchers from Switzerland’s Ecole polytechnique federale de Lausanne (EPFL) have done just that with their new invention.
Researchers from Nanyang Technological University, Singapore (NTU Singapore) have developed the capability to use recycled glass in 3D printing, opening doors to a more environmentally sustainable way of building and construction.
Glass is one material that can be 100% recycled with no reduction in quality, yet it is one of the least recycled waste types. Glass is made up of silicon dioxide, or silica, which is a major component of sand, and therefore it offers significant untapped potential to be recycled into other products.
At the same time, due to growing populations, urbanization and infrastructure development, the world is facing a shortage of sand, with climate scientists calling it one of the greatest sustainability challenges of the 21st century.
BLACKSBURG, Va. (WFXR) – As housing prices across the country continue to skyrocket, an Iowa-based company, Alquist 3D, is looking to combat the crisis by 3D-printing homes.
Alquist, one of a few U.S. companies that 3D-prints houses, is looking to build 200 of these homes in Virginia starting this summer.
The process is somewhat simple. First, a person designs what they want the frame of the house to look like by using a computer program. Then, a file is transmitted to a machine, which tells it what to do and how to move.
Researchers at the University of Freiburg have worked with colleagues at the University of California, Berkeley to come up with a novel means of rapidly 3D printing complex glass parts at a microscopic scale.
Known as ‘Microscale Computed Axial Lithography’ (Micro-CAL), this approach involves exposing resin to 2D light images of a desired shape from multiple angles, which when they overlap, trigger polymerization. When used to print the Glassomer material previously honed at Freiburg, the team say their layer-free process has the potential to unlock devices with new microfluidic or micro-optical functionality.
“For the first time, we were able to print glass with structures in the range of 50 micrometers in just a few minutes, which corresponds roughly to the thickness of a hair,” explains the University of Freiburg’s Dr. Frederik Kotz-Helmer. The ability to manufacture such components at high speed and with great geometric freedom will enable new functions and more cost-effective products in the future.”