3D printing can deliver massive savings in time taken to build the house exteriors, shaving off weeks from the process.
Category: 3D printing – Page 36
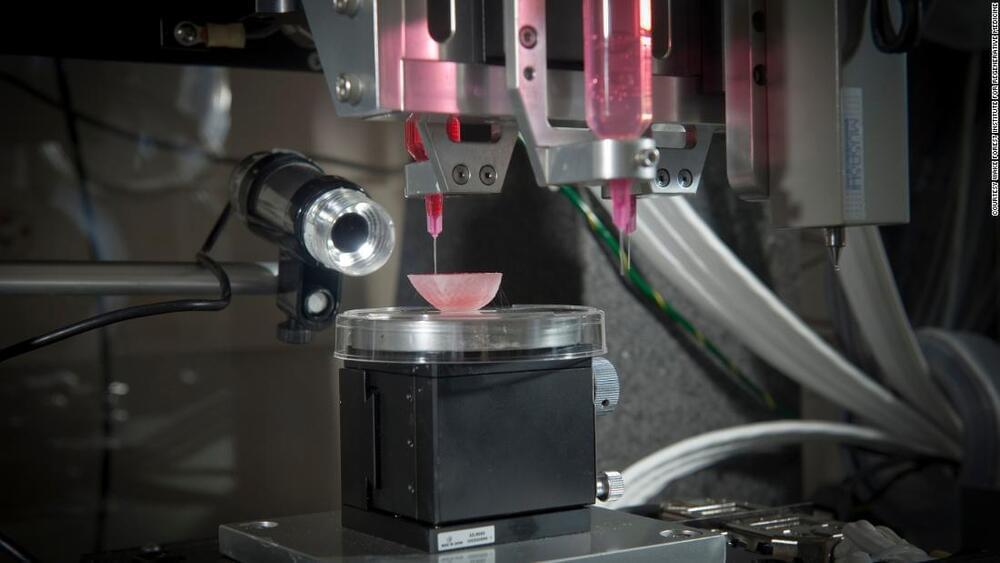
When we’ll be able to 3D-print organs and who will be able to afford them
To begin the process of bioprinting an organ, doctors typically start with a patient’s own cells. They take a small needle biopsy of an organ or do a minimally invasive surgical procedure that removes a small piece of tissue, “less than half the size of a postage stamp,” Atala said. “By taking this small piece of tissue, we are able to tease cells apart (and) we grow and expand the cells outside the body.”
This growth happens inside a sterile incubator or bioreactor, a pressurized stainless steel vessel that helps the cells stay fed with nutrients – called “media” – the doctors feed them every 24 hours, since cells have their own metabolism, Lewis said. Each cell type has a different media, and the incubator or bioreactor acts as an oven-like device mimicking the internal temperature and oxygenation of the human body, Atala said.
“Then we mix it with this gel, which is like a glue,” Atala said. “Every organ in your body has the cells and the glue that holds it together. Basically, that’s also called ‘extracellular matrix.’”.
New type of 3D printing uses sound waves to build up objects
“Ultrasonic frequencies are already being used in destructive procedures like laser ablation of tissues and tumours,” said Prof. Muthukumaran Packirisamy, who led the study along with Dr. Mohsen Habibi and PhD student Shervin Foroughi. “We wanted to use them to create something.”
For instance, utilizing the technique, aircraft mechanics could conceivably 3D-print repairs onto internal components, without opening the plane’s fuselage. It’s even possible that implants could be 3D printed within a patient’s body, without the need for surgery.
Besides the PDMS resin, the scientists have also successfully used DSP to print objects made of ceramic material. They now plan on experimenting with polymer-metal composites, followed by pure metal.
3D printing typically involves depositing layers of molten plastic, laser-melting powdered metal, or using UV light to harden gelatinous resin. A new technique takes yet another approach, however, by utilizing sound waves.
Developed by a team of scientists at Canada’s Concordia University, the technology is known as direct sound printing (DSP).
In the current version of the technique, a transducer is used to send focused pulses of ultrasound through the sides of a chamber, into liquid polydimethylsiloxane (PDMS) resin contained within. Doing so produces ultrasonic fields, which cause rapidly oscillating microscopic bubbles to temporarily form at specific points in the resin.
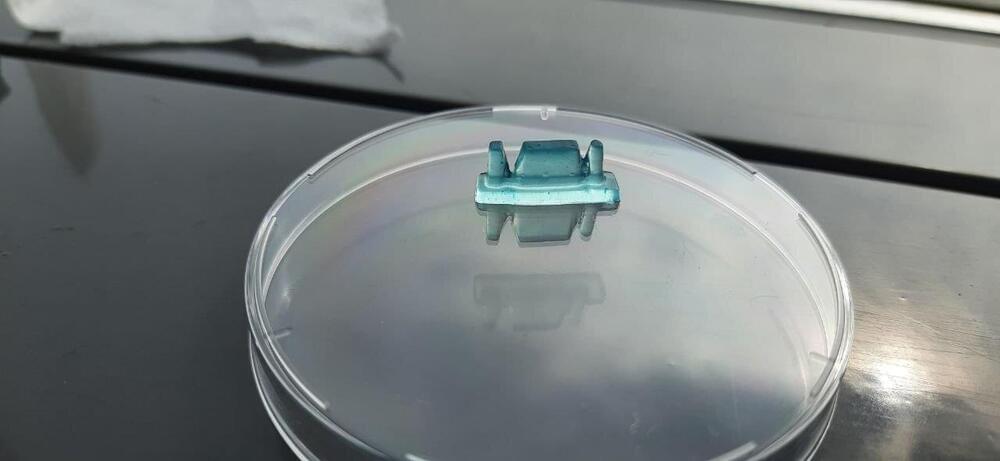
New natural hydrogel inks for digital light processing 3D printing
Researchers at Politecnico di Torino, BRIN in Indonesia, the Italian Institute of Technology (IIT) and University of Cagliari have recently introduced new composite hydrogel inks based on natural and environment friendly materials, which could be used to 3D print objects. These hydrogels, presented in a paper published in Sustainable Materials and Technologies, are based on acrylated-carboxymethyl cellulose (mCMC).
“We have been working on the development of new printable materials and functional devices since 2015, so in these years different areas were explored, resulting in many publications in the field of 3D printing,” Ignazio Roppolo, one of the researchers who carried out the study, told TechXplore.
The first objective of the work by Roppolo and his colleagues was to develop polymeric hydrogels for 3D printing that are based on natural resources, to increase sustainability and reduce the use of standard synthetic resins. In recent years, the team has been collaborating with Dr. Athanasia Amanda Septevani, a researcher at BRIN’s Research Center for Environment and Clean Technology in Indonesia.
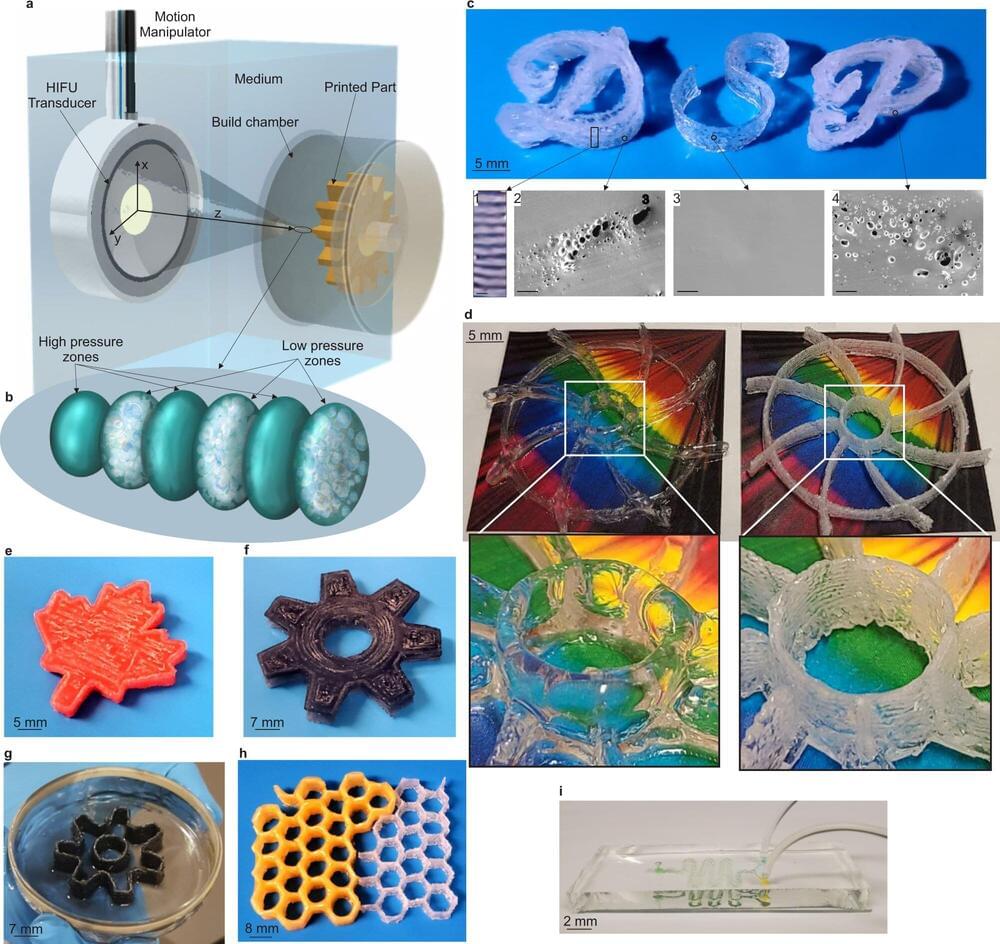
Direct sound printing is a potential game-changer in 3D printing, according to researchers
Most 3D printing methods currently in use rely either on photo (light)- or thermo (heat)-activated reactions to achieve precise manipulation of polymers. The development of a new platform technology called direct sound printing (DSP), which uses soundwaves to produce new objects, may offer a third option.
The process is described in a paper published in Nature Communications. It shows how focused ultrasound waves can be used to create sonochemical reactions in minuscule cavitation regions—essentially tiny bubbles. Extremes of temperature and pressure lasting trillionths of a second can generate pre-designed complex geometries that cannot be made with existing techniques.
“Ultrasonic frequencies are already being used in destructive procedures like laser ablation of tissues and tumors. We wanted to use them to create something,” says Muthukumaran Packirisamy, a professor and Concordia Research Chair in the Department of Mechanical, Industrial and Aerospace Engineering at the Gina Cody School of Engineering and Computer Science. He is the paper’s corresponding author.
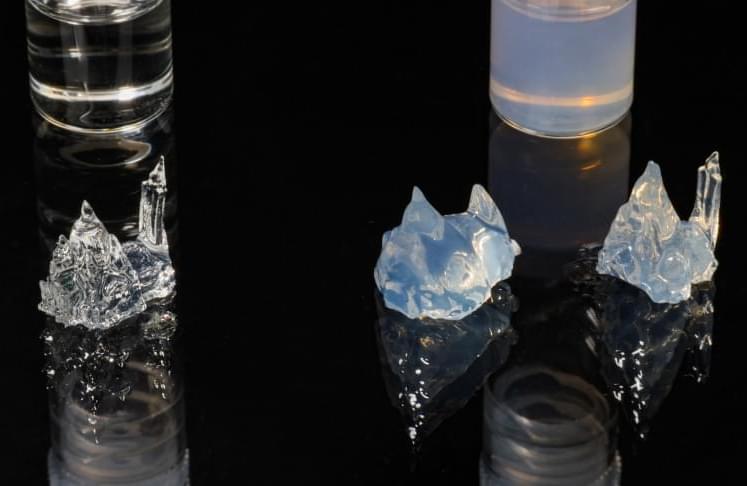
A novel 3D printing technique produces objects out of resin in mere seconds
Engineers at EPFL’s Laboratory of Applied Photonic Devices (LAPD), within the School of Engineering, have developed a novel 3D printer capable of fabricating objects almost instantaneously in opaque resin, according to a press release by the institution published on Monday.
EPFL claims its new 3D printer is one of the fastest in the world. It achieves this speed by replacing additive manufacturing with a new volumetric method.
A Star Wars-inspired test
“We pour the resin into a container and spin it,” said in a statement Christophe Moser, a professor at LAPD. “Then we shine light on the container at different angles, causing the resin to solidify wherever the accumulated energy in the resin exceeds a given level. It’s a very precise method and can produce objects at the same resolution as existing 3D-printing techniques.”

Scientists Can Now Fully 3D-Print Wood In A Lab — Without Cutting Any Trees
Biodiversity is on the verge of being devastated due to the inclination towards deforestation these days. The adverse climatic conditions that our Earth is facing nowadays are also the result of this pressing concern. However, to mitigate this climatic distress caused by deforestation, a team of researchers at the MIT Institute has come up with a novel technique to artificially grow wood in a controlled environment in the lab, which can then be used for making furniture and other wooden houses, which are now being made from cutting trees, thereby posing a threat to our natural habitat. Apart from the amazing growth, we can also print “3D custom-designed wooden structures” out of the replicas, which can considerably reduce wood waste as well.
Prior to discussing the mechanism of wood production, an interesting thing to note is that we can easily change the shape and structure of these artificially produced woods according to our requirements. The researchers have demonstrated the whole process through an experiment in which a flowering plant known as “Common zinnia (Zinnia Elegans)” would be taken and the cells are then extracted from its leaves which can then be conserved in a liquid mixture for several days. After it becomes nutritionally embellished, a gel-based material would be utilized to further refine the mixture.
However, these cells would then give birth to new plant cells which will then be treated accordingly as per the lab conditions. Moreover, we can also reform the physical and mechanical properties of the cells by increasing or decreasing the hormonal concentrations as per the needs.
Scientists 3D print human tissue in space
A new bioprinter is proven to work in space. Researchers demonstrated they could 3D print human tissue cells on the International Space Station.
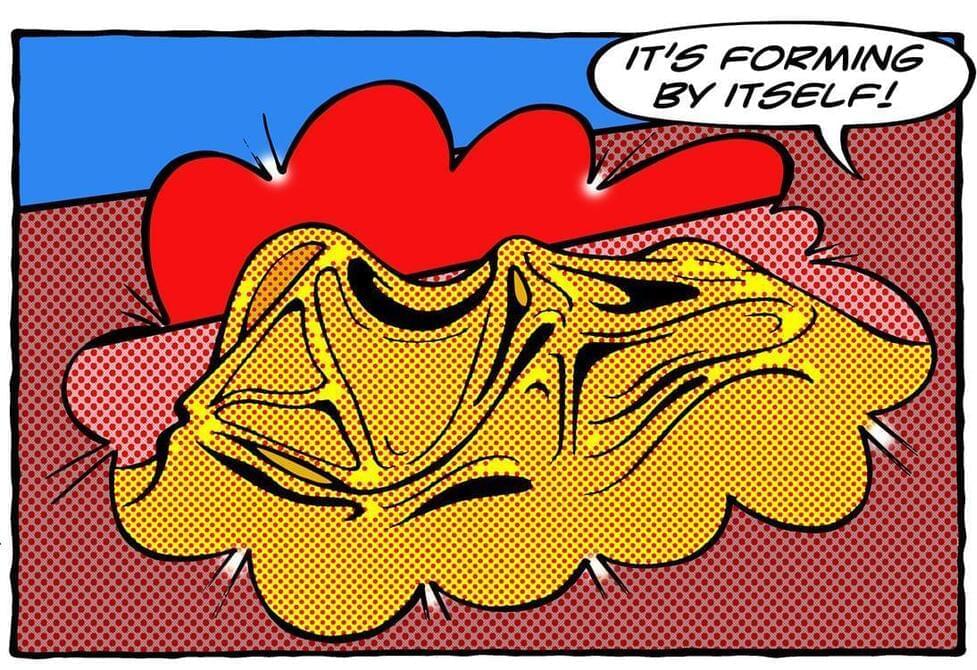
3D printing adds another dimension
Nina Notman learns how 4D printing is opening the door to unique smart materials whose applications may only be limited by our imaginations.
Smart materials are already part of our daily lives. From novelty mugs with thermochromic pigments that change colour when holding a hot drink, to photochromic prescription glasses’ lenses that darken when the sun is out, to hydrogels that expand to soak up liquid in disposable nappies and period products. But these are only the tip of the iceberg in terms of what smart materials – that can sense information about the environment around them and then act accordingly – are predicted to achieve in the future.
According to a recent Royal Society report, smart materials on the way include window glass that changes porosity in response to humidity, clothing that adapts to environmental conditions and self-healing concretes. ‘Animate materials could eventually have a transformative effect on all spheres of life,’ the report authors wrote.
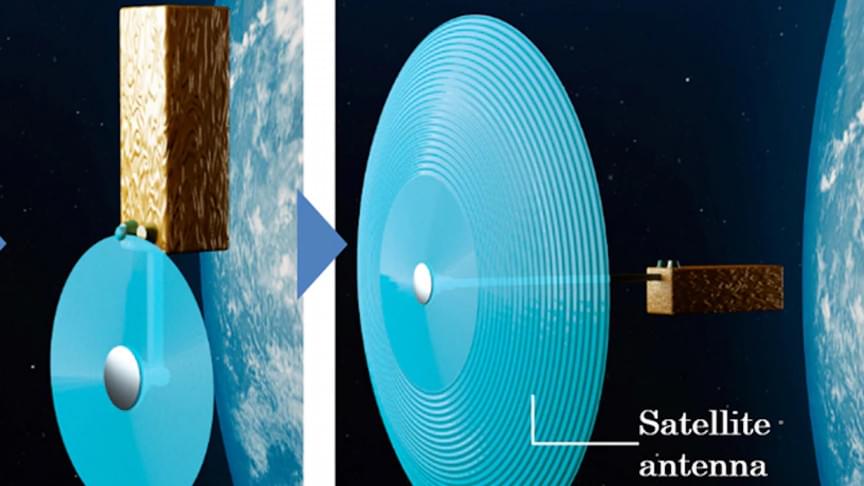
Satellite antennas could be 3D printed in space to massively reduce launch costs
“Spacecraft antenna designs are challenging due to their conflicting requirements for high gain, wide bandwidth, and low weight,” Mitsubishi announced. “High gain and wide bandwidth necessarily require a large aperture, but economical orbital deployment conventionally dictates that designs be lightweight and small enough to fit or fold inside a launch vehicle or satellite deployment mechanism.”
Mitsubishi also claimed that, with its new technology, ‘additive-manufacturing in space has now become possible.’ However, it’s worth noting that the International Space Station already features a 3D printer launched to the orbital station back in 2014. The European Space Agency also announced last year it would experiment with 3D printing in space using scrap metals from the Moon.
Still, the company’s new method has the potential to reduce the cost of satellite launches significantly, and it could pave the way for the construction of other vital parts for future space missions.