Learn more ➡ https://fcld.ly/lng297f
Category: robotics/AI – Page 1,539
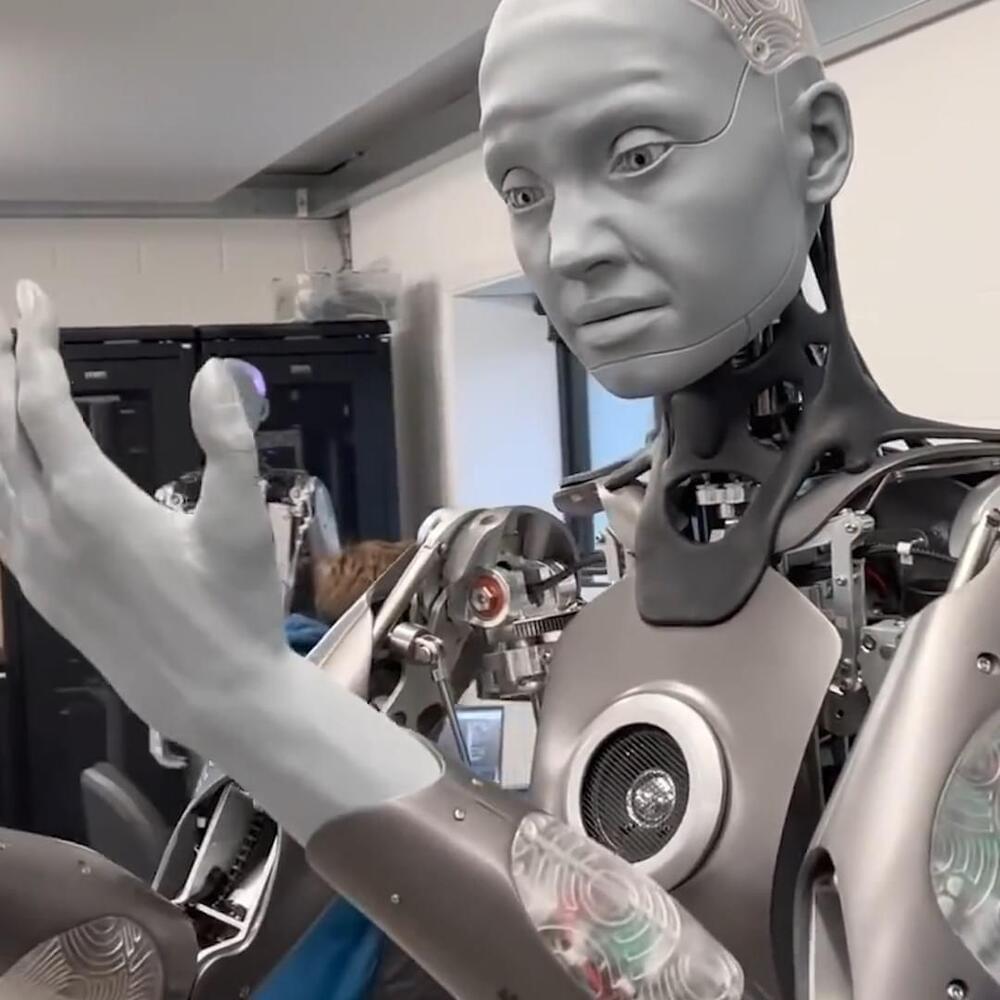
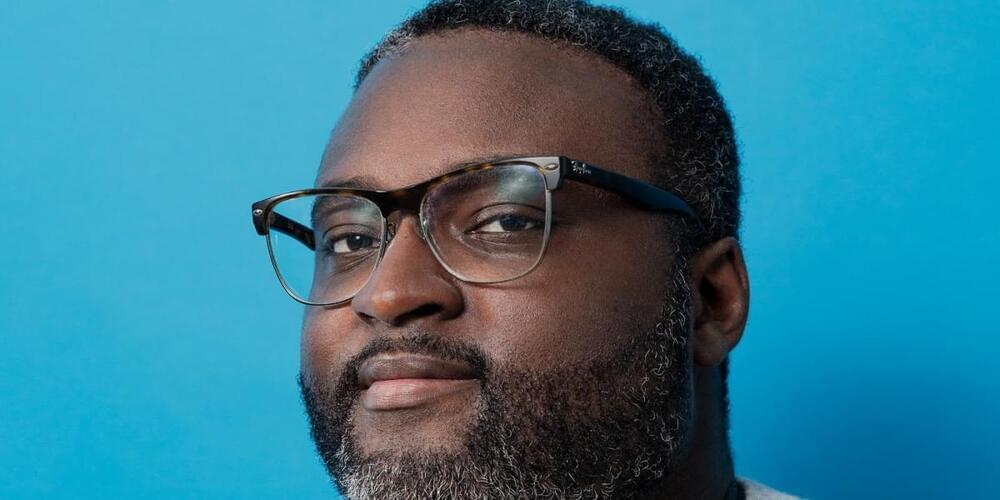
The true dangers of AI are closer than we think
As long as humans have built machines, we’ve feared the day they could destroy us. Stephen Hawking famously warned that AI could spell an end to civilization. But to many AI researchers, these conversations feel unmoored. It’s not that they don’t fear AI running amok—it’s that they see it already happening, just not in the ways most people would expect.
AI is now screening job candidates, diagnosing disease, and identifying criminal suspects. But instead of making these decisions more efficient or fair, it’s often perpetuating the biases of the humans on whose decisions it was trained.
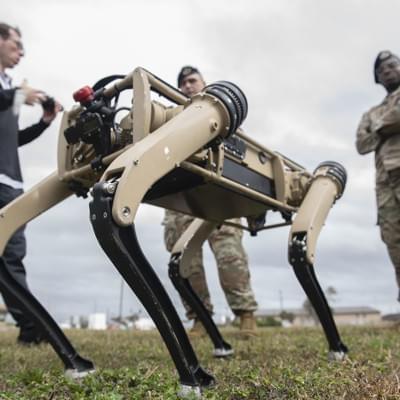
New AI medical program can spot rare diseases
BONN, Germany — When you’re sick, you can often see it in your face that you’re not feeling well. For rare diseases, it’s usually not that easy. However, researchers in Germany say artificial intelligence may change all that. A team from the University of Bonn say a new facial analysis program can actually detect the warning signs of rare diseases by examining the features of a person’s face.
“The goal is to detect such diseases at an early stage and initiate appropriate therapy as soon as possible,” says Prof. Dr. Peter Krawitz from the Institute for Genomic Statistics and Bioinformatics (IGSB) at the University Hospital Bonn in a university release.

Tesla News | Boston Dynamics to supply army of robots for DHL | High Tech News
👉For business inquiries: [email protected].
✅ Instagram: https://www.instagram.com/pro_robots.
You’re on the PRO Robots channel and in this video we bring you the latest in high-tech news. Jetpack racing, boots for walking through the meta universe, drones for fruit picking, Tesla and Boston Dynamics, new DARPA competitions and other high-tech news in one issue!
0:00 In this video.
0:20 Cargo hybrid drone.
1:02 Tesla News.
1:50 Transportation to explore the moon and Mars.
2:34 Boston Dynamics News.
3:14 Surgery performed by a robot.
4:07 Meta Company.
4:50 Red Bull 2022 Contest.
5:22 Cost effectiveness of robotaxis.
6:15 Drones for inspection.
6:48 DARPA.
7:58 Drone fruit picking.
8:29 Shoes for the metaverse.
9:15 New type of robotic grippers.
9:44 A submarine with 2 arms.
10:20 A drone that launches with a cannon.
10:49 Company Motorica.
#prorobots #robots #robot #futuretechnologies #robotics.
More interesting and useful content:
✅ Elon Musk Innovation https://www.youtube.com/playlist?list=PLcyYMmVvkTuQ-8LO6CwGWbSCpWI2jJqCQ
✅Future Technologies Reviews https://www.youtube.com/playlist?list=PLcyYMmVvkTuTgL98RdT8-z-9a2CGeoBQF
✅ Technology news.
https://www.facebook.com/PRO.Robots.Info.
#prorobots #technology #roboticsnews.
Robotic birth simulator saves lives in the delivery room
Those uncanny valley in eyes effect should be changed.
These medical professionals are delivering babies from a robotic birth simulator to prepare for life-and-death situations in the hospital room.
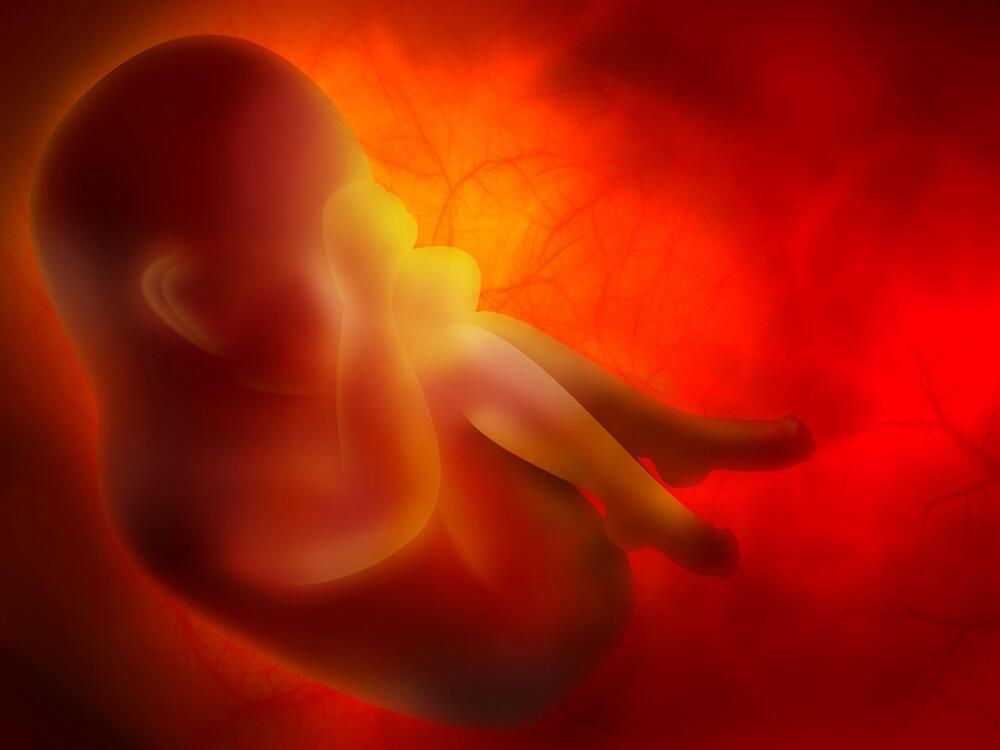
Stephen Hawking Predicted a Race of ‘Superhumans’ To Take Over the World
Stephen Hawking made terrifying predictions of the future. Based on science, the late British physicists predicted several things that could happen on Earth, from the rise of powerful Artificial intelligence to fearful robots poised to destroy humankind. Hawking also spoke about how it was dangerous to search for aliens and how global warming could destroy Earth as we know it.
However, Stephen Hawking also spoke about how abrupt advances in genetic science could lead to creating a future generation of superhumans that could eventually destroy humanity as we know it.
In recently published papers, Prof. Hawking predicted that an elite class of physically altered, intellectually powerful humans could come into existence from rich people choosing to edit their existing DNA and manipulate future generations’ genetic markup.
(Part II) Supercentenarian (112 — 116y) Blood Test Analysis
Join us on Patreon!
https://www.patreon.com/MichaelLustgartenPhD
Papers referenced in the video:
Main study:
Clinical course of the longest-lived man in the world: A case report.
https://pubmed.ncbi.nlm.nih.gov/34973348/
Commonly used clinical chemistry tests as mortality predictors: Results from two large cohort studies.
https://pubmed.ncbi.nlm.nih.gov/33152050/
Predicting age by mining electronic medical records with deep learning characterizes differences between chronological and physiological age.
https://pubmed.ncbi.nlm.nih.gov/29113935/
The gamma gap predicts 4-year all-cause mortality among nonagenarians and centenarians.
https://pubmed.ncbi.nlm.nih.gov/29348636/
Implication of liver enzymes on incident cardiovascular diseases and mortality: A nationwide population-based cohort study.