The futuristic gizmo will launch this month.
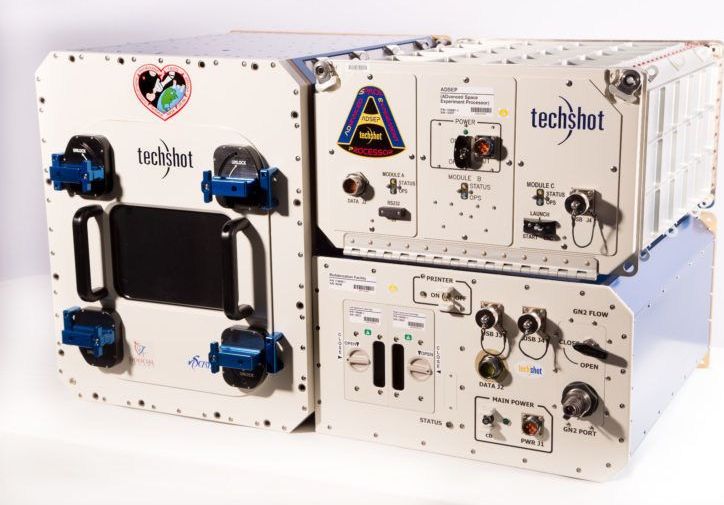
Kyle Reese: The Terminator’s an infiltration unit, part man, part machine. Underneath, it’s a hyperalloy combat chassis — micro processor-controlled, fully armored. Very tough. But outside, it’s living human tissue — flesh, skin, hair, blood, grown for the cyborgs…
3D bioprinting is the automated fabrication of multicellular tissue via spatially defined deposition of cells. The ability to spatially control deposition in the x, y and z axes allows for creation of tissue-specific patterns or compartments, with in vivo-like architecture that mimics key aspects of native biology.
3D bioprinted tissues exhibit a microenvironment more suited to in vivo-like cellular function in comparison to traditional 2D monoculture (or monolayer co-cultures), as well as maintenance of a more defined architecture than is observed in self-aggregated co-culture models.
“One of the biggest roadblocks to generating functional tissue replacements has been our inability to print the complex vasculature that can supply nutrients to densely populated tissues,” said Jordan Miller, assistant professor at Rice University in the US.
“Further, our organs actually contain independent vascular networks — like the airways and blood vessels of the lung or the bile ducts and blood vessels in the liver,” Miller said.
“These interpenetrating networks are physically and biochemically entangled, and the architecture itself is intimately related to tissue function. Ours is the first bioprinting technology that addresses the challenge of multi vascularisation in a direct and comprehensive way,” he said.
The cosmos are filled with roughly Earth-sized exoplanets. Various moons, comets, and planets have stores of water, organic molecules, and amino acids like those that make up life on Earth.
Cathal O’Donnell, a 3D bioprinting researcher at St. Vincent’s Hospital in Melbournethose odds — he argues in The Conversation that the abundance of potentially habitable worlds out there makes the discovery of extraterrestrial life “inevitable and possibly imminent.”
In an effort to scale up the manufacture of biomaterials, researchers at UC Berkeley have combined bioprinting, a robotic arm, and flash freezing in a method that may one day allow living tissue, and even whole organs, to be printed on demand. By printing cells into 2D sheets and then freezing them as assembled, the new technique improves cell survival during both building and storage.
(3D-printed heart scaffold)
As the head of the University of Illinois Urbana-Champaign’s innovative Cancer Center, Bhargava has been plugging away at injecting more advanced engineering solutions into medical problems. The freeform 3D printer is one of the first futuristic achievements of that effort.
But Bhargava’s project is just one of a wave of technologies that stand to transform medicine and healthcare as we know it; to make them faster, more accurate, and hopefully, drastically more affordable. Microneedle patches, handheld diagnostic machines, and better sensing capabilities, as well as 3D bioprinting, are just a few of the technologies coming to a doctor’s office near you—or maybe even into your home—in the next decade.