The future of bioprinting looks promising from a technical and scientific perspective, but it’s far from clear how it will be regulated.
Category: 3D printing – Page 59
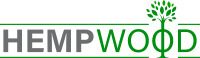
Home: Apparently people are cool with lumber as an industry, as opposed to lumber as a carbon collector
Choice is the one thing our creators gave us. Me, personally I prefer hemp, and not just because I smoke the female version for medicinal reasons, but because scientifically it makes sense, and can help unscrew #AmericanFarmers…Yes we need more forests, not less. However, we don’t need to use trees, when we have hemp. Pembient can 3D Print ivory, thus making animal Ivory obsolete, yet people still kill for Ivory. We can make wood products from hemp, yet we still fell trees. #HowDumbAreWe
Eco-Friendly Our hemp is grown using sustainable methods, which helps eliminate deforestation.
Made in the USA All hemp growth and material production is conducted in the United States of America.
Multiple Uses HempWood can.
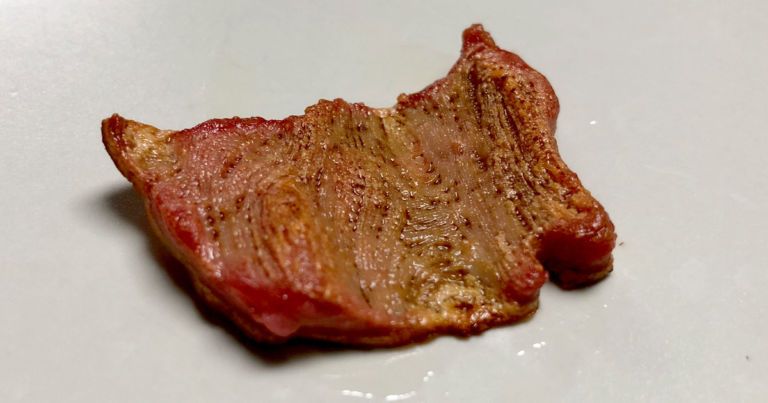
World’s First 3D-Printed Heart Could Revolutionize Organ Transplants
Many of you are way ahead of me on this topic. I design 3D printed parts for aircraft, but I didn’t think that functional, transplantable 3D printed human organs were this advanced. This article is about a heart, but it is currently only the size of a rabbit heart. Sizing it up to human size and testing are next, but this is much farther along than I expected.
Rapid creation of replacement organs, using the patient’s own cells to circumvent the body rejecting the transplant, is a direct contributor to superlongevity.
Researchers from Tel Aviv University have created the world’s first 3D printed heart, using cellular materials from the patient.
Researchers find a way to 3D print whole objects in seconds
When you think of 3D printing, you probably imagine a structure being created layer by layer, from the bottom up. Now, researchers from Switzerland’s Ecole polytechnique fédérale de Lausanne (EPFL) say they have developed a completely new way of creating 3D objects that offer remarkable resolution “in record time.”
As EPFL News reports, the method draws on the principle of tomography — the technique for displaying a representation of a cross section through a solid object, using x-rays or ultrasound. To make an object, a photosensitive resin is illuminated from multiple angles, with the accumulation of light helping to solidify the resin. In other words, the object forms a solid structure within the resin in one go, rather than segment by segment, as is the case with traditional 3D printing.
The World’s First 3D-Printed Heart Model
This is the first-ever 3D-printed human heart model using human cells #ValentinesDay
3D Printing Is Changing the World | VICE on HBO
3D-printing innovations in recent years have brought a sea change in the fabrication of everything from automobile parts to human bio-tissues.
VICE’s Krishna Andavolu delves into the cutting-edge research behind what’s being called the next industrial revolution, meeting the scientists and entrepreneurs pushing the boundaries of manufacturing, material science, and even space exploration.
Check out VICE News for more: http://vicenews.com
Follow VICE News here:
Facebook: https://www.facebook.com/vicenews
Twitter: https://twitter.com/vicenews
Tumblr: http://vicenews.tumblr.com/
Instagram: http://instagram.com/vicenews
More videos from the VICE network: https://www.fb.com/vicevideo
#VICEonHBO
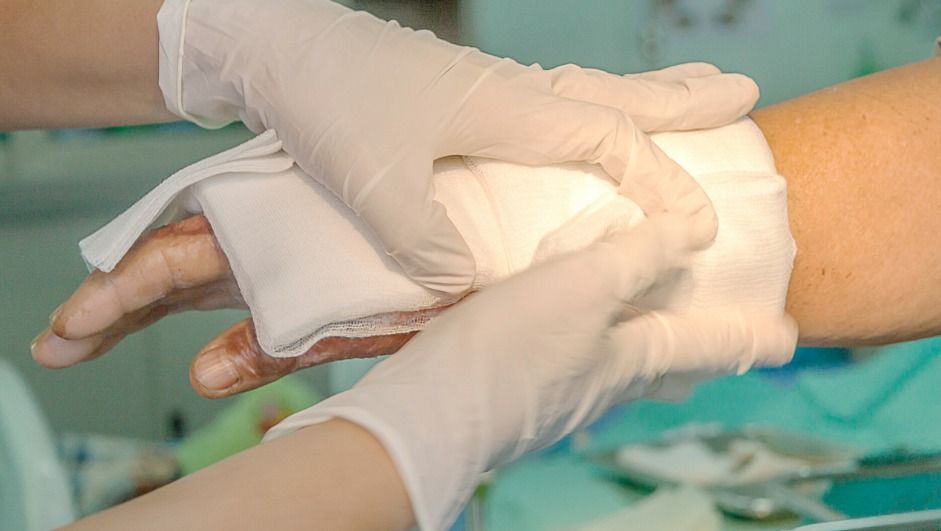
Handheld bioprinter for treating burns at the point-of-care
A burn that is over 25% of the human body area can be life threatening. However a burn that is only 1 percent but on a visible area of the body can be life-worsening. That is why advancements in the area of wound care and burns treatment are so important from patient perspective. Being a doctor of the future will include having a point-of-care device such as a 3D-Bioprinter that will scan the lesions in dept and width and print a gel imbued with cells and prolo-factors.
Forgive me my conservatism… we already have such clinics that are on the clinical trials for such treatments.
Read more in the article. Stay tuned for more topics through the Academy blog. Gain more knowledge in Regenerative Medicine and practical experience with biologics through the Annual Congress — Global Regenerative Congress 18–20 September 2020 in Dubai. Registrations are open: www.grc2020dubai.com
Researchers from the University of Toronto (ON, Canada) have reported success in trials of a handheld bioprinter for treating serious burns and wounds.
Handheld Skin 3D Printer Can Help Burn Victims
This handheld 3D printer deposits layers of skin tissue, and could one day help to heal deep wounds. Instead of waiting for skin patches to grow in a Petri dish, you apply it directly.
A team of Canadian scientists has successfully applied skin tissue to burn wounds using a handheld 3D printer. This technology may become a game-changer in the way severe burn victims are treated.
The handheld skin 3D printer, the work of scientists at the University of Toronto Engineering and Sunnybrook Hospital, was first shown back in 2018. Since then it has undergone a major redesign that improves upon the initial model’s functionality.
3D Printed Human Corneas To Cure Blindness Are Here
Scientists at Newcastle University, in the United Kingdom, have 3D printed the world’s first real human corneas. This is unbelievable news since today, there is a significant shortage of corneas available for transplant. In the future, this printing technique could be used to ensure an unlimited supply of corneas.
The cornea is the outermost layer of the human eye and it has an important role in focusing vision. Statistics show that there are currently 10 million people worldwide requiring surgery to prevent corneal blindness as a result of diseases such as trachoma, an infectious eye disorder. On top of that, there are an additional 5 million people who suffer total blindness due to corneal scarring caused by burns, lacerations, abrasion or disease.