MIT neuroscientists have made a breakthrough in treating fragile X syndrome by leveraging a novel neurotransmitter signaling pathway. By targeting a specific subunit of NMDA receptors, they successfully reduced excessive protein synthesis in the brain, a hallmark of the disorder. Their approach, tested in fragile X model mice, not only corrected molecular imbalances but also improved synaptic function and reduced disease symptoms.
Get the latest international news and world events from around the world.
80-Megapixel Masterpiece Captures a Cosmic Nursery Bursting With Color and Energy
A breathtaking new image of the RCW 38 star cluster showcases a cosmic nursery bursting with color, light, and energy.
Located 5,500 light-years away, this region teems with young, newly formed stars and swirling clouds of glowing gas. The European Southern Observatory’s powerful VISTA telescope cuts through the dust to reveal hidden celestial wonders, offering astronomers a rare glimpse into the chaotic beauty of star birth.
A stunning glimpse of RCW 38.
This Gravitational-Wave Breakthrough Could Rewrite What We Know About the Universe
A new adaptive optics technology is set to transform gravitational-wave detection, allowing LIGO
LIGO, or the Laser Interferometer Gravitational-Wave Observatory, is a large-scale physics experiment and observatory to detect cosmic gravitational waves and to develop gravitational-wave observations as an astronomical tool. There are two LIGO observatories in the United States—one in Hanford, Washington, and the other in Livingston, Louisiana. These observatories use laser interferometry to measure the minute ripples in spacetime caused by passing gravitational waves from cosmic events, such as the collisions of black holes or neutron stars.
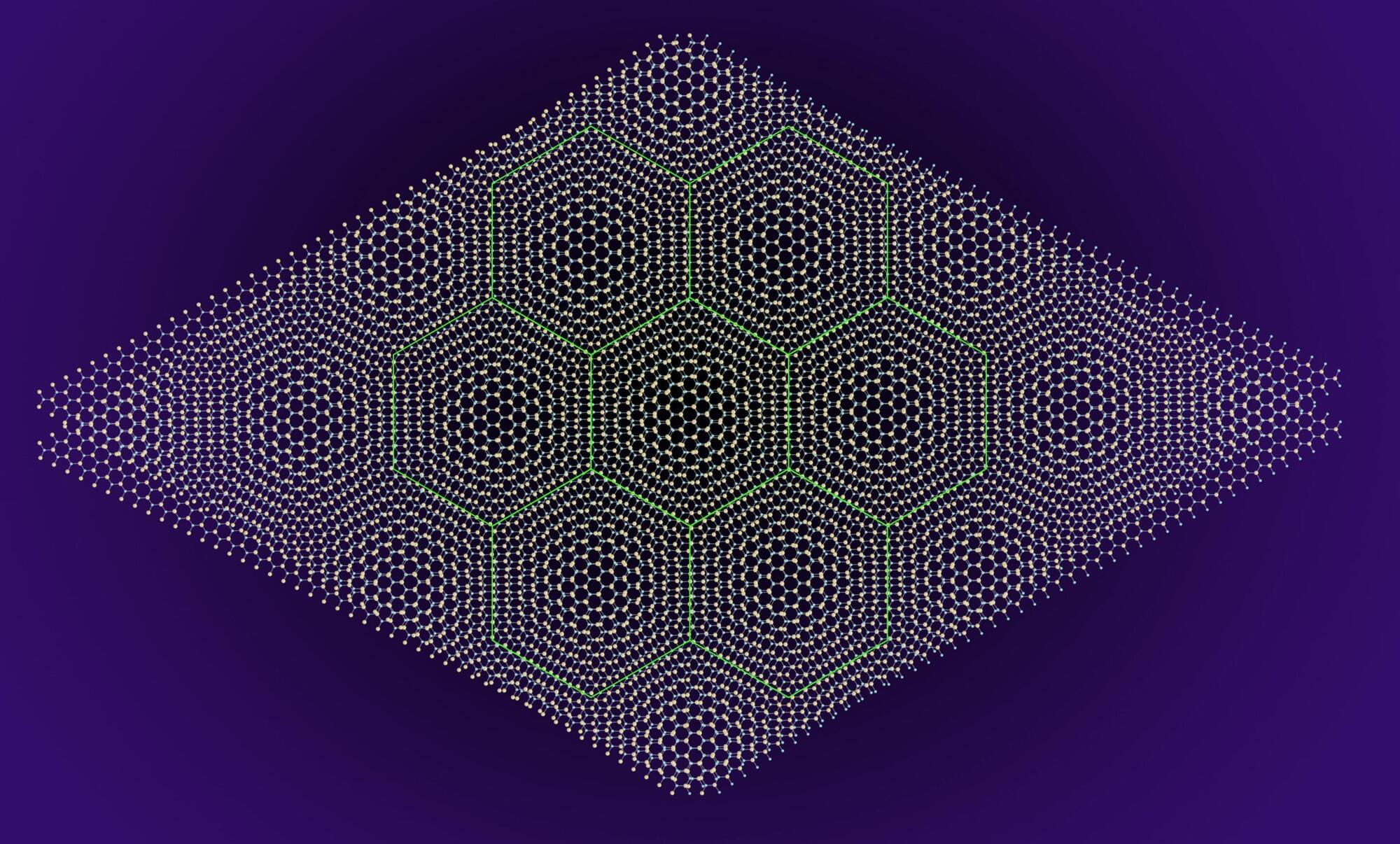
Advancing quantum materials: A new approach to controlling electronic states
A collaborative team of researchers from the Max Planck Institute for Structure and Dynamics of Matter (MPSD), Nanjing University, Songshan Lake Materials Laboratory (SLAB), and international partners has introduced a new method to regulate exotic electronic states in two-dimensional materials.
Building on the foundations laid by their previous work on twisted van der Waals materials, the team of physicists has now discovered a novel way to manipulate correlated electronic states in twisted double bilayer tungsten diselenide (TDB-WSe₂). This breakthrough offers new possibilities for developing advanced quantum materials and devices.
By precisely twisting two bilayers of WSe₂ near a 60-degree angle and applying a perpendicular electric field, the researchers have achieved control over the interaction between two distinct electronic bands, known as the K-valley and Γ-valley bands. This tuning has led to the observation of a “valley charge-transfer insulator”—an exotic state where electron movement is highly correlated, and electrical conductivity is suppressed.
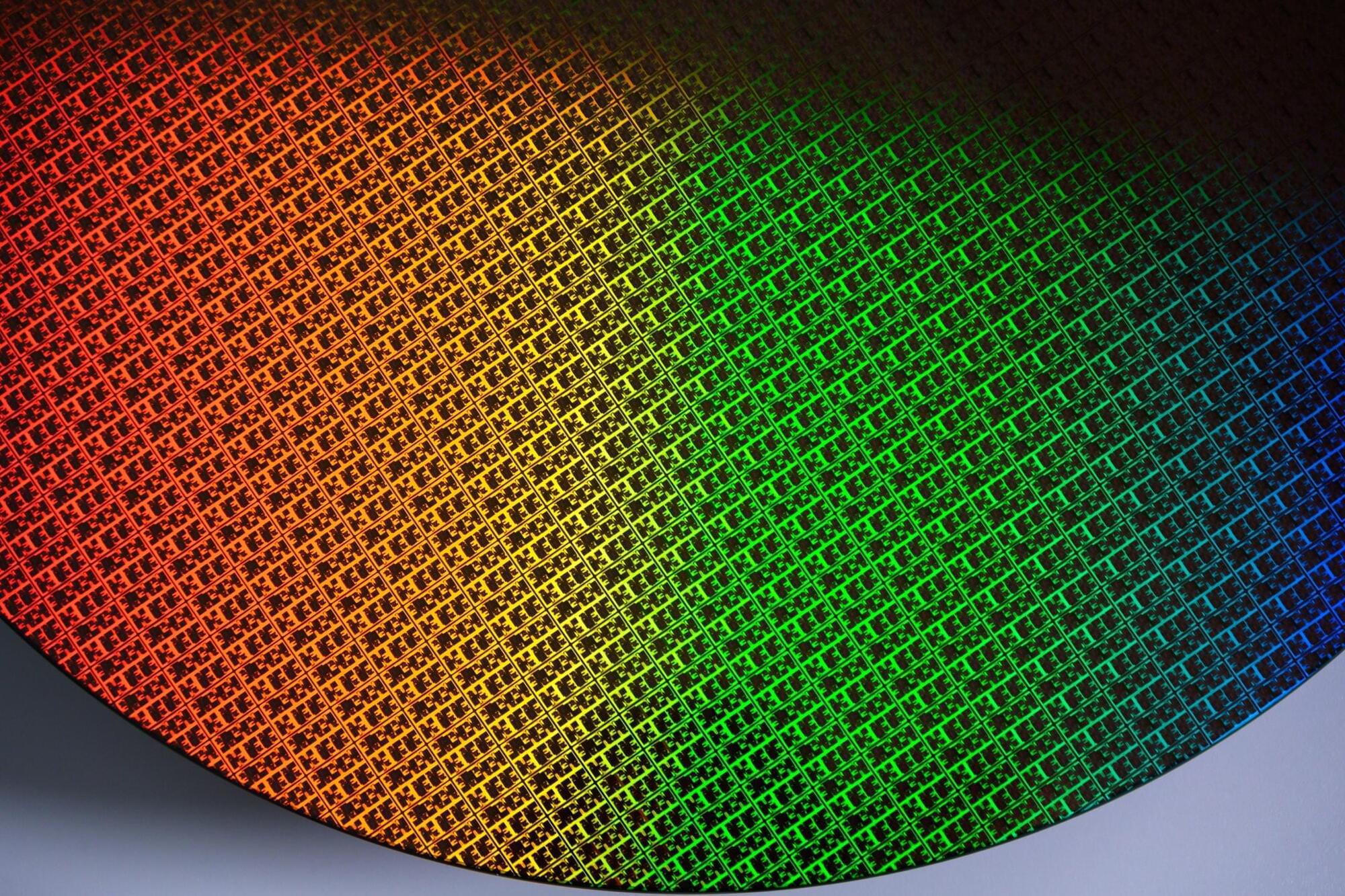
Intel’s 18A Process Reportedly Comes With SRAM Density On-Par With TSMC’s N2; Team Blue Gearing Up For A Phenomenal Comeback
Intel’s 18A is said to report an SRAM density equal to that of TSMC’s N2 process, signaling a massive breakthrough for the IFS and its semiconductor ambitions.
Intel’s 18A Process Is a “Special” One, Credits To Implementations Such As BSPDN Along With Years of R&D Behind It
Well, it seems like now might be the time to be bullish on the future of Intel’s chip plans, since the latest reports are clearly indicating that the momentum is shifting towards Team Blue. Following the political backing of the Trump administration, it is now disclosed via ISSCC sessions (via Ian Cutress) that both TSMC and Intel’s cutting-edge processes are rivaling each other in SRAM densities, showing that the gap has been narrowed down significantly, at least in one of the important aspects.
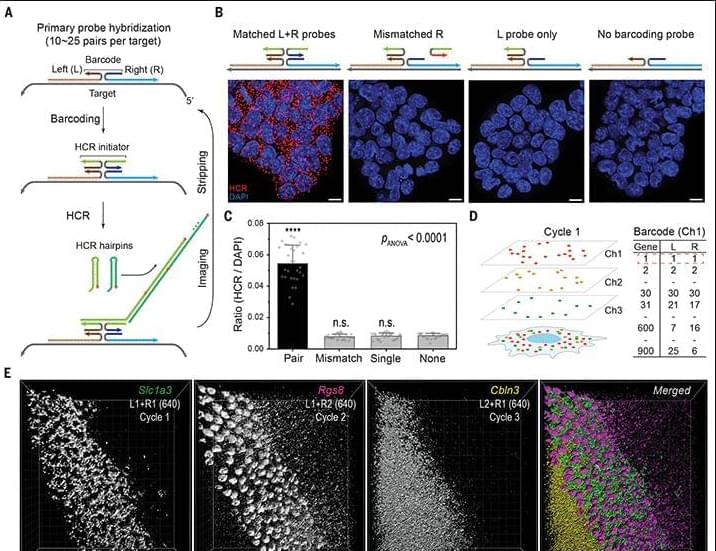
Deep-tissue transcriptomics and subcellular imaging at high spatial resolution
Limited color channels in fluorescence microscopy have long constrained spatial analysis in biological specimens. Here, we introduce cycle Hybridization Chain Reaction (HCR), a method that integrates multicycle DNA barcoding with HCR to overcome this limitation. cycleHCR enables highly multiplexed imaging of RNA and proteins using a unified barcode system. Whole-embryo transcriptomics imaging achieved precise three-dimensional gene expression and cell fate mapping across a specimen depth of ~310 μm. When combined with expansion microscopy, cycleHCR revealed an intricate network of 10 subcellular structures in mouse embryonic fibroblasts. In mouse hippocampal slices, multiplex RNA and protein imaging uncovered complex gene expression gradients and cell-type-specific nuclear structural variations.
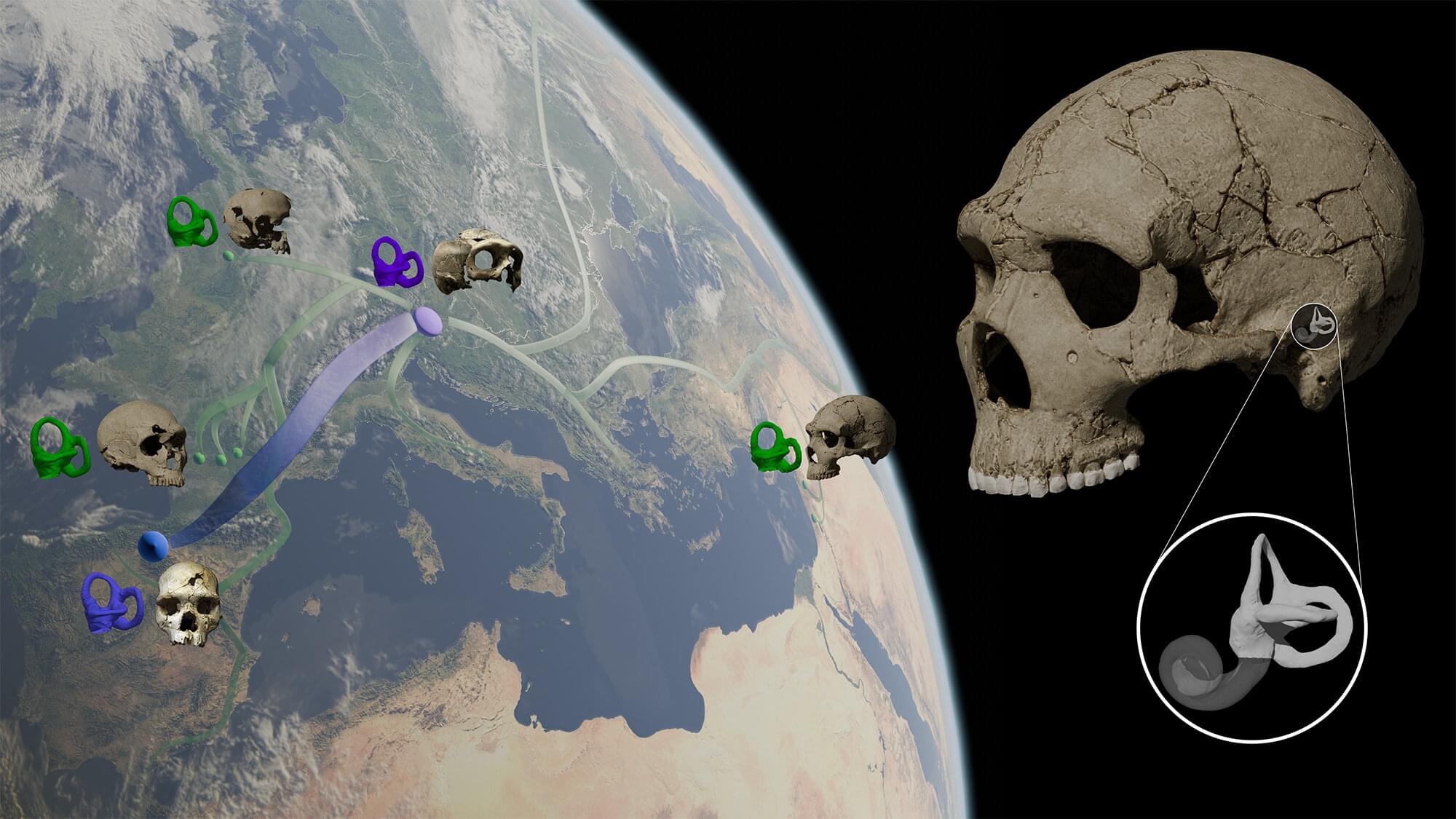
The inner ear of Neanderthals reveals clues about their enigmatic origin
New research on the inner ear morphology of Neanderthals and their ancestors challenges the widely accepted theory that Neanderthals originated after an evolutionary event that implied the loss of part of their genetic diversity. The findings, based on fossil samples from Atapuerca (Spain) and Krapina (Croatia), as well as from various European and Western Asian sites have been published in Nature Communications.
Neanderthals emerged about 250,000 years ago from European populations—referred to as “pre-Neanderthals”—that inhabited the Eurasian continent between 500,000 and 250,000 years ago. It was long believed that no significant changes occurred throughout the evolution of Neanderthals, yet recent paleogenetic research based on DNA samples extracted from fossils revealed the existence of a drastic genetic diversity loss event between early Neanderthals (or ancient Neanderthals) and later ones (also referred to as “classic” Neanderthals).
Technically known as a “bottleneck,” this genetic loss is frequently the consequence of a reduction in the number of individuals in a population. Paleogenetic data indicate that the decline in genetic variation took place approximately 110,000 years ago.
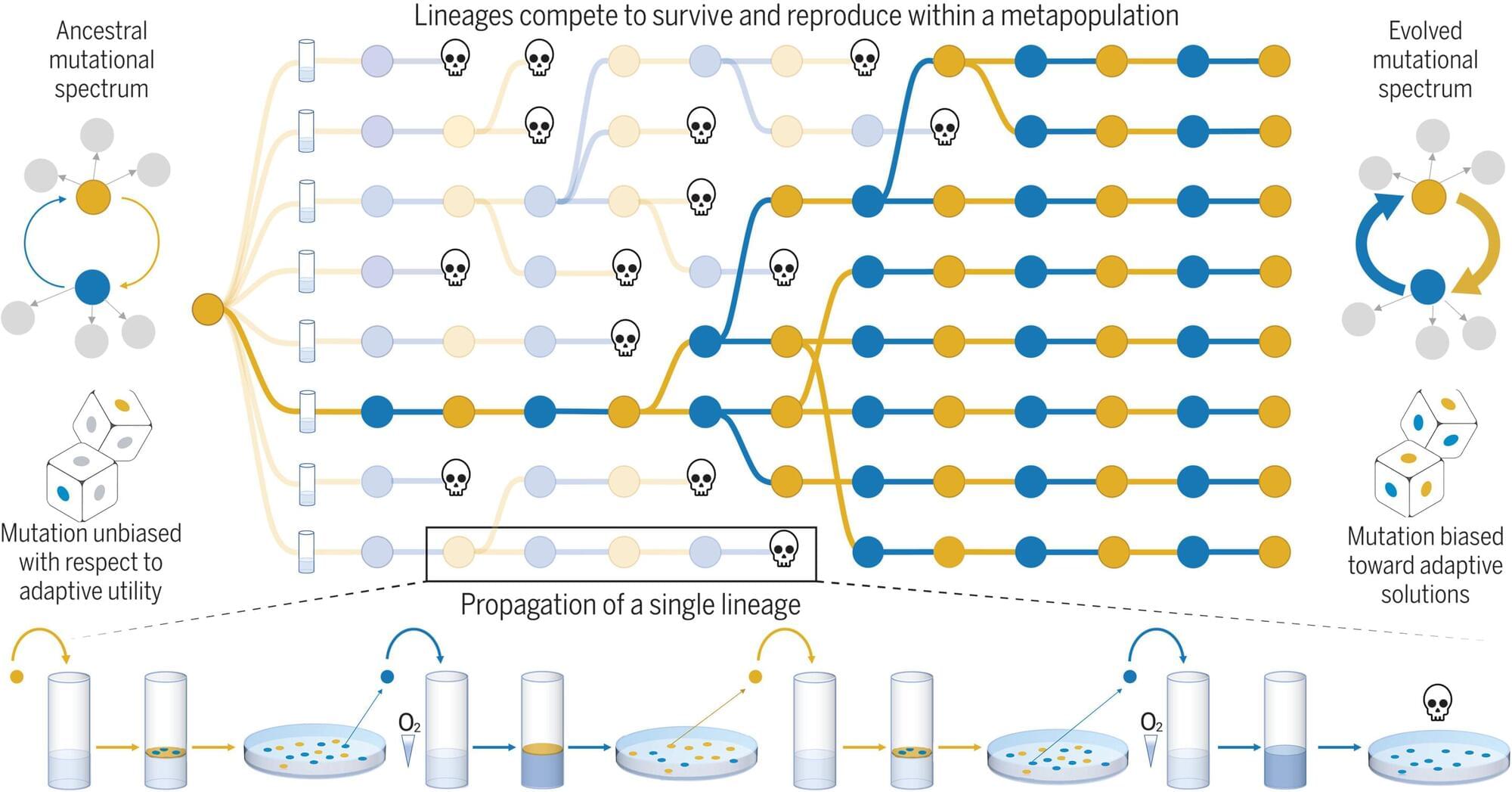
Insights into evolutionary dynamics: Study reveals the evolution of evolvability
A new study by researchers at the Max Planck Institute for Evolutionary Biology (MPI-EB) sheds fresh light on one of the most debated concepts in biology: evolvability. The work provides the first experimental evidence showing how natural selection can shape genetic systems to enhance future capacity for evolution, challenging traditional perspectives on evolutionary processes.
The research is published in the journal Science. A related Perspective article also appears in Science.
The ability of organisms to generate adaptive genetic variation is crucial for evolutionary success, particularly in changing environments. The MPI-EB study investigates whether natural selection operates not merely as a “blind” process driven by random mutations but could actively favor mechanisms that channel mutations toward adaptive outcomes.
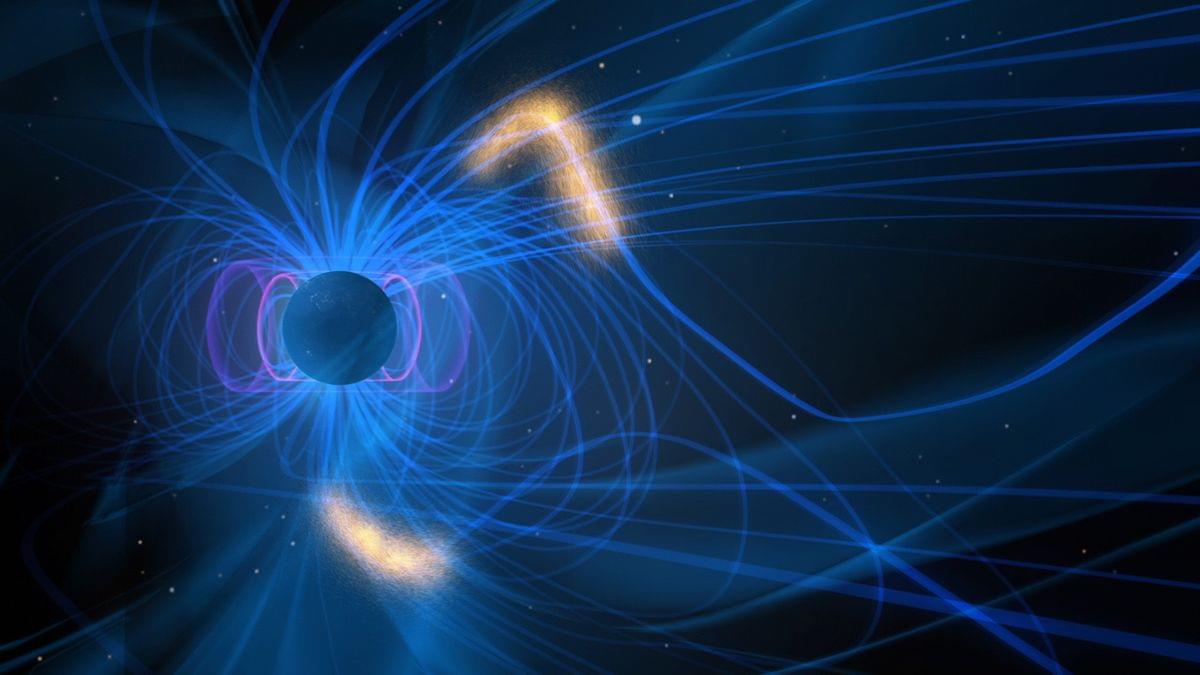
NASA satellites catch Earth’s magnetic field making music
And understanding these waves a little better could help scientists better predict when and where they’ll happen, as well as how strong they’ll be. That could be vital to the safety of satellites orbiting our planet, which are vulnerable to solar storms and other sudden bursts of radiation from deep space.
“These high-energy electrons are known as ‘killer electrons’ because they have damaged several satellites, costing hundreds of millions of dollars,” wrote Horne. “Chorus waves are now included in forecasting models that are designed to protect these satellites.”
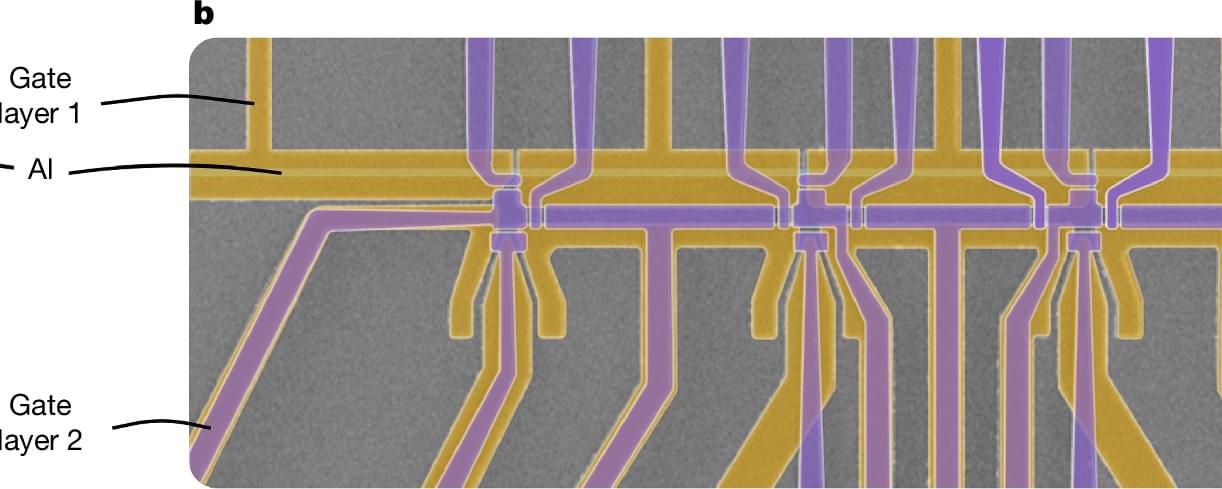
Microsoft (Again) Claims Topological Quantum Computing With Majorana Zero Mode Anyons
As the fundamental flaw of today’s quantum computers, improving qubit stability remains the focus of much research in this field. One such stability attempt involves so-called topological quantum computing with the use of anyons, which are two-dimensional quasiparticles. Such an approach has been claimed by Microsoft in a recent paper in Nature. This comes a few years after an earlier claim by Microsoft for much the same feat, which was found to be based on faulty science and hence retracted.
The claimed creation of anyons here involves Majorana fermions, which differ from the much more typical Dirac fermions. These Majorana fermions are bound with other such fermions as a Majorana zero mode (MZM), forming anyons that are intertwined (braided) to form what are in effect logic gates. In the Nature paper the Microsoft researchers demonstrate a superconducting indium-arsenide (InAs) nanowire-based device featuring a read-out circuit (quantum dot interferometer) with the capacitance of one of the quantum dots said to vary in a way that suggests that the nanowire device-under-test demonstrates the presence of MZMs at either end of the wire.
Microsoft has a dedicated website to their quantum computing efforts, though it remains essential to stress that this is not a confirmation until their research is replicated by independent researchers. If confirmed, MZMs could provide a way to create more reliable quantum computing circuitry that does not have to lean so heavily on error correction to get any usable output. Other, competing efforts here include such things as hybrid mechanical qubits and antimony-based qubits that should be more stable owing to their eight spin configurations.