MIT researchers devise new technique to visualize the internal forces within granular materials in intricate 3D detail.
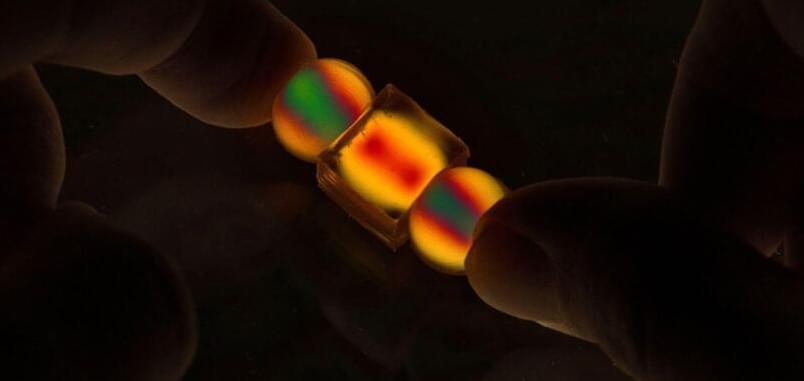
To enhance this efficiency, there is a requirement to fabricate electrodes with a porous structure. Unfortunately, existing technologies face challenges in achieving a uniform coating of ceramic materials within electrodes possessing intricate porous structures.
A collaborative research team, comprising Professor Jihwan An and Ph.D. candidate Sung Eun Jo from the Department of Mechanical Engineering at Pohang University of Science and Technology (POSTECH), and others, has successfully produced porous electrodes for SOFCs using latest semiconductor processes. This research has been featured as a back cover article in Small Methods.
The process of atomic layer deposition (ALD) involves depositing gaseous materials onto a substrate surface in thin, uniform atomic layers. In a recent study, Professor Jihwan An’s team, known for their prior work in enhancing the efficiency of SOFCs using ALD, developed and applied a powder ALD process and equipment. This enabled them to precisely coat nano-thin films on fine powders.
Scientists have scarcely begun studying pristine material from asteroid Bennu brought back to Earth by the OSIRIS-REx mission, but have already found several surprises.
Researchers at AMOLF, in collaboration with partners from Germany, Switzerland, and Austria, have realized a new type of metamaterial through which sound waves flow in an unprecedented fashion. It provides a novel form of amplification of mechanical vibrations, which has the potential to improve sensor technology and information processing devices.
“For the first time we have shown that even a tiny fraction of cellular material could be identified by a mass spectrometer onboard a spacecraft,” said Dr. Fabian Klenner.
How will we find life on Jupiter’s icy moon, Europa, and Saturn’s icy moon, Enceladus? This is what a recent study published in Science Advances hopes to address as a team of international researchers investigate how ice grains that are discharged from the active plumes of these small moons could possess enough organic material for life to exist. This study holds the potential to help astrobiologists develop the necessary instruments and methods to find life on these small moons, specifically with NASA’s Europa Clipper scheduled to launch this October, whose goal will be to investigate Europa’s habitability potential.
Artist’s illustration of Saturn’s moon, Enceladus, seen here upside down as the plumes are on the south pole. (Credit: NASA/JPL-Caltech)
Image of Jupiter’s moon, Europa, obtained in natural light by NASA’s Juno spacecraft. (Credit: NASA/JPL-Caltech/SwRI/MSSS/Kevin M. Gill)
For the study, the researchers conducted laboratory experiments to simulate how future instruments could fly through the plumes to safely detect bacterial cells, even within one ice grain. The goal was to ascertain if one ice grain was sufficient in detecting bacterial cells as opposed to collecting bulk samples of ice grains. The researchers chose to investigate Sphingopyxis alaskensis, which is a known bacterium that resides off the coast of Alaska, due to its small size and ability to survive in cold environments with little nutrients. In the end, the researchers found they could detect this simple bacterium in a single ice grain using current instruments, including an advanced version of the SUrface Dust Analyzer onboard Europa Clipper.