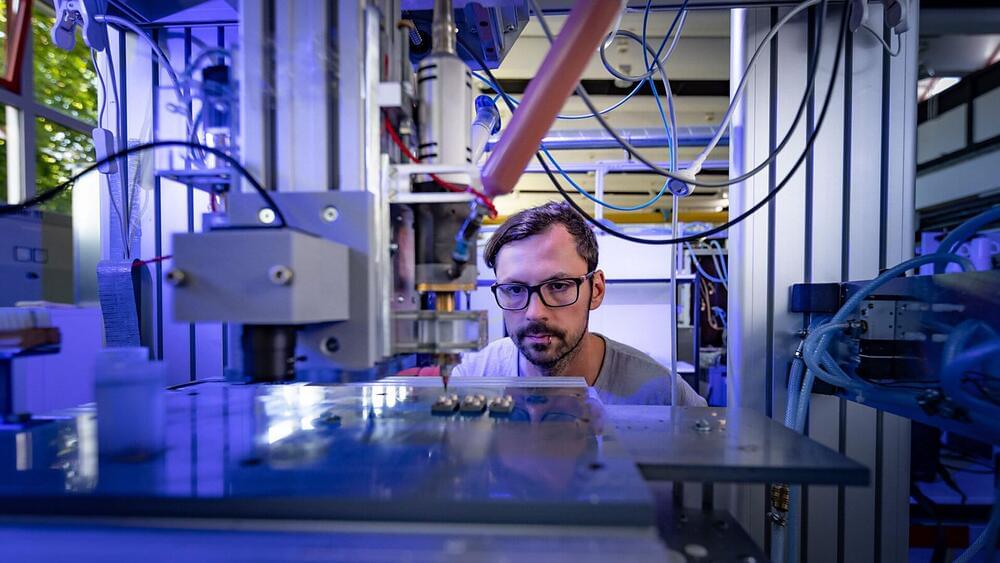
Researchers at the Professorship of Electrical Energy Conversion Systems and Drives at Chemnitz University of Technology have succeeded for the first time in 3D printing housings for power electronic components that are used, for example, to control electrical machines. During the printing process, silicon carbide chips are positioned at a designated point on the housing.
As with the printed motor made of iron, copper and ceramics, which the professorship first presented at the Hannover Messe in 2018, ceramic and metallic pastes are also used in the 3D printing of housings. “These are sintered after the printing process, together—and this is what makes them special—with the imprinted chip,” says Prof. Dr. Ralf Werner, head of the Professorship of Electrical Energy Conversion Systems and Drives. Ceramic is used as an insulating material and copper is used for contacting the gate, drain and source areas of the field-effect transistors. “Contacting the gate area, which normally has an edge length of less than one millimeter, was particularly challenging,” adds Prof. Dr. Thomas Basler, head of the Professorship of Power Electronics, whose team supported the project with initial functional tests on prototypes.
Following the ceramic-insulated coils printed at Chemnitz University of Technology, which were presented at the Hannover Messe in 2017, and the printed motor, drive components that can withstand temperatures above 300 °C are now also available. “The desire for more temperature-resistant power electronics was obvious, because the housings for power electronic components are traditionally installed as close as possible to the engine and should therefore have an equally high temperature resistance,” says Prof. Werner.