Saudi find may reveal how humans harnessed early dogs to survive
Get the latest international news and world events from around the world.

Brain-to-voice neuroprosthesis restores naturalistic speech
AI-based model streams intelligible speech from the brain in real time

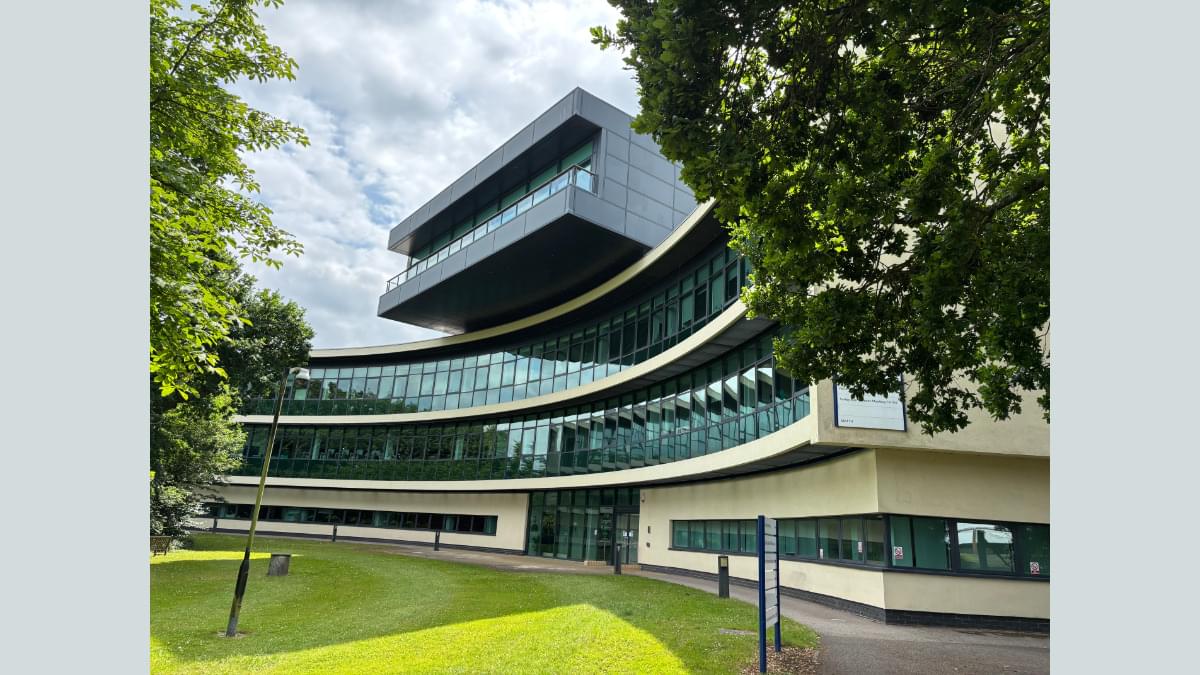
Prostate cancer vaccine research launched University of Surrey
In September 2025, The Prostate Project, a Guildford-based volunteer-led charity, will launch a £250,000 campaign to raise funds for a prostate cancer research project widely anticipated to be ‘game-changing’
Work has begun to develop a vaccine to prevent the return of prostate cancer in men who have undergone a radical prostatectomy, the surgical removal of the prostate. Cancer vaccines have become an exciting area of research in recent years, and this new treatment could potentially save the lives of more than 1,500 men each year in the UK alone.
The Prostate Project, based at the Stokes Centre for Urology at Royal Surrey County Hospital, has a proven track record of funding research and treatment of prostate cancer, raising more than £11 million since its formation in 1998.
Some of these cookies are necessary and are used to help make our site work. With your consent, we will also use cookies to improve your experience, analyse site usage and assist in our marketing efforts. By clicking ‘Accept all’, you consent to our use of cookies.
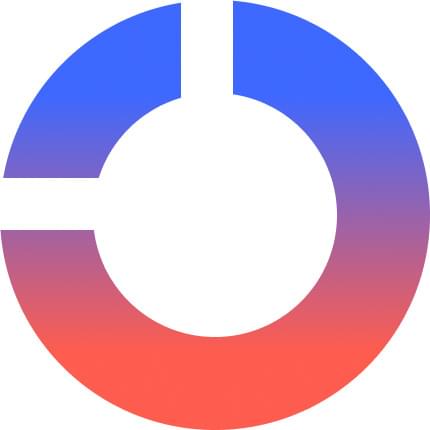
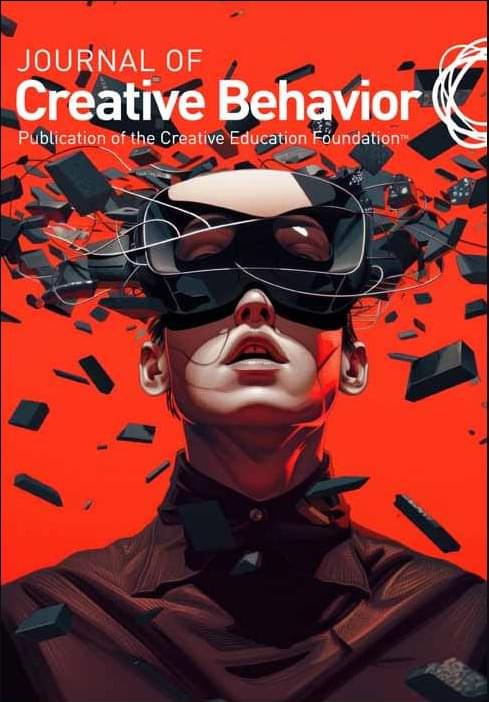
The Different Relationships Between Mobile Phone Dependence and Adolescents’ Scientific and Artistic Creativity: Self‐Esteem and Creative Identity as Mediators
Creativity is the ability to generate original, useful, and meaningful ideas or solutions by combining imagination with knowledge and experience. It involves flexible, divergent thinking and seeing connections that others might overlook.
Artistic creativity refers to expressing ideas, emotions, or concepts through mediums such as painting, music, writing, or performance, emphasizing aesthetic and emotional impact.
Scientific creativity, on the other hand, involves problem-solving, hypothesis generation, and innovative experimentation that can advance knowledge or technology.
The Different Relationships Between Mobile Phone Dependence and Adolescents’ Scientific and Artistic Creativity: Self-Esteem and Creative Identity as Mediators.
Creativity is an essential skill that is at the heart of 21st-century education. Mobile phone use occupies considerable amounts of time in people’s lives and may influence creativity. However, few studies have linked mobile phone dependence (MPD) to adolescents’ domain-specific creativity (science and art). This study investigated the relationship between MPD and the scientific and artistic creativity of 2,922 adolescents (10–15 years old) by using the Test of Mobile Phone Dependence, the Middle School Students’ Everyday Creativity Questionnaire, the Rosenberg Self-Esteem Scale, and the Short Scale of Creative Self, all self-reported measures. Specifically, linear regression analysis and segmented regression analysis were conducted to explore the relationships between MPD and scientific and artistic creativity.
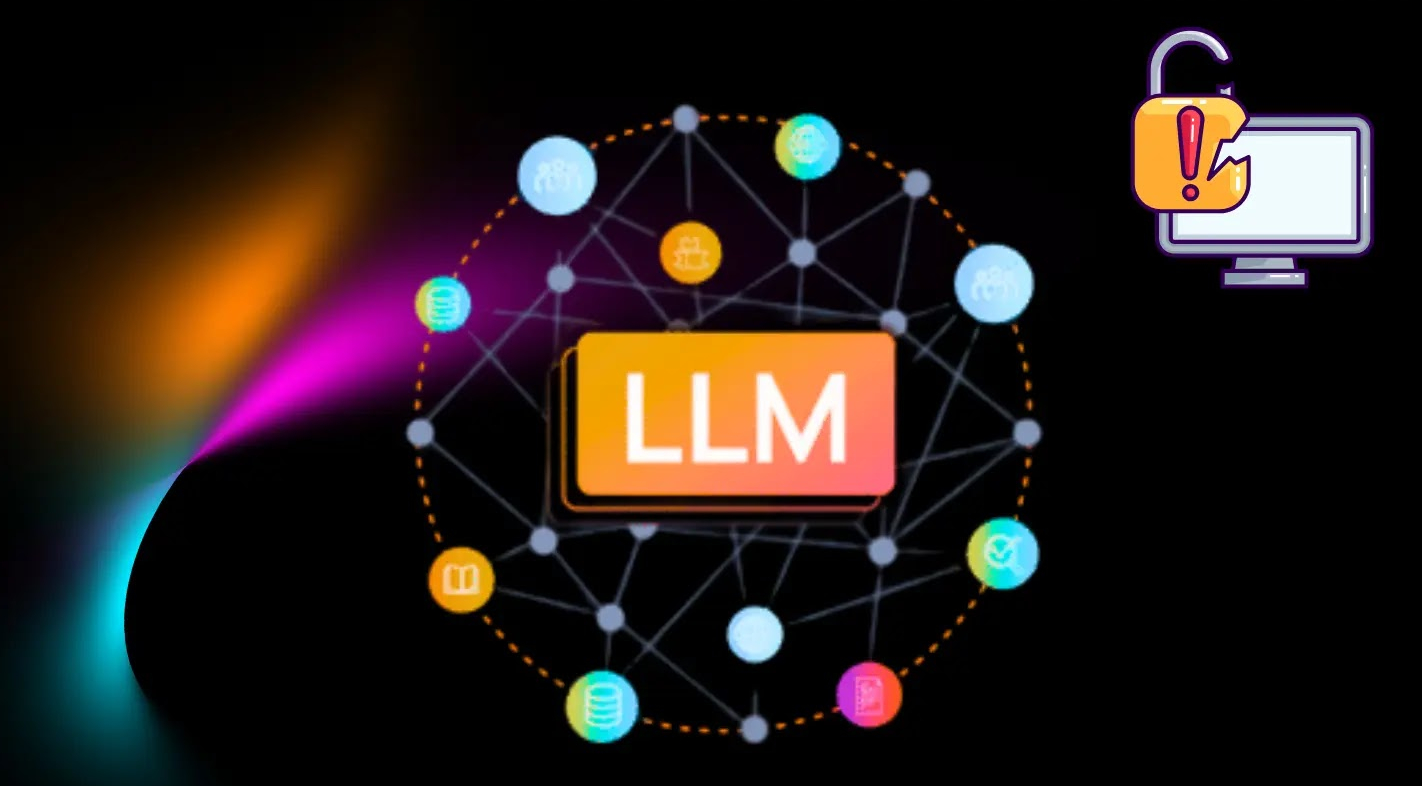
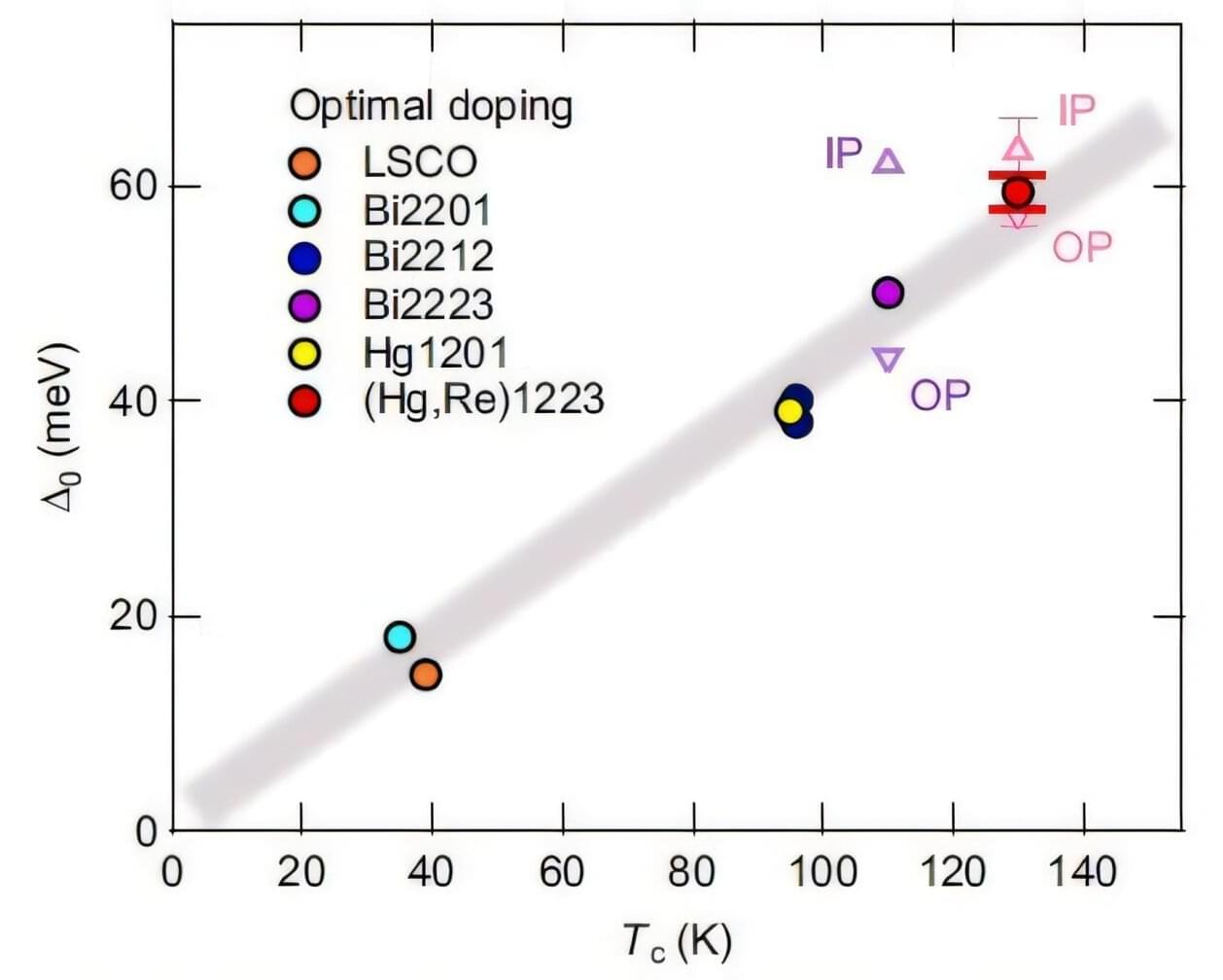
Uncovering the mysteries of high-temperature cuprate superconductors
In their quest to explore and characterize high-temperature superconductors, physicists have mostly focused on a material that is not the absolute highest. That’s because that crystal is much easier to split into uniform, easily measurable samples. But in 2024, researchers found a way to grow good crystals that are very similar to the highest temperature superconductor.
Now, many from the same group have analyzed these new crystals and determined why the highest temperature superconductor is indeed higher and what details were missed by looking at the more popular crystal. Their work is published in Physical Review Letters.
The cuprate Bi2223, which at ambient pressure (about 100,000 pascals) superconducts at 110 Kelvin (−163°C), has proven easier to study and specify, even though the similar cuprate Hg1223 superconducts at 134 K.
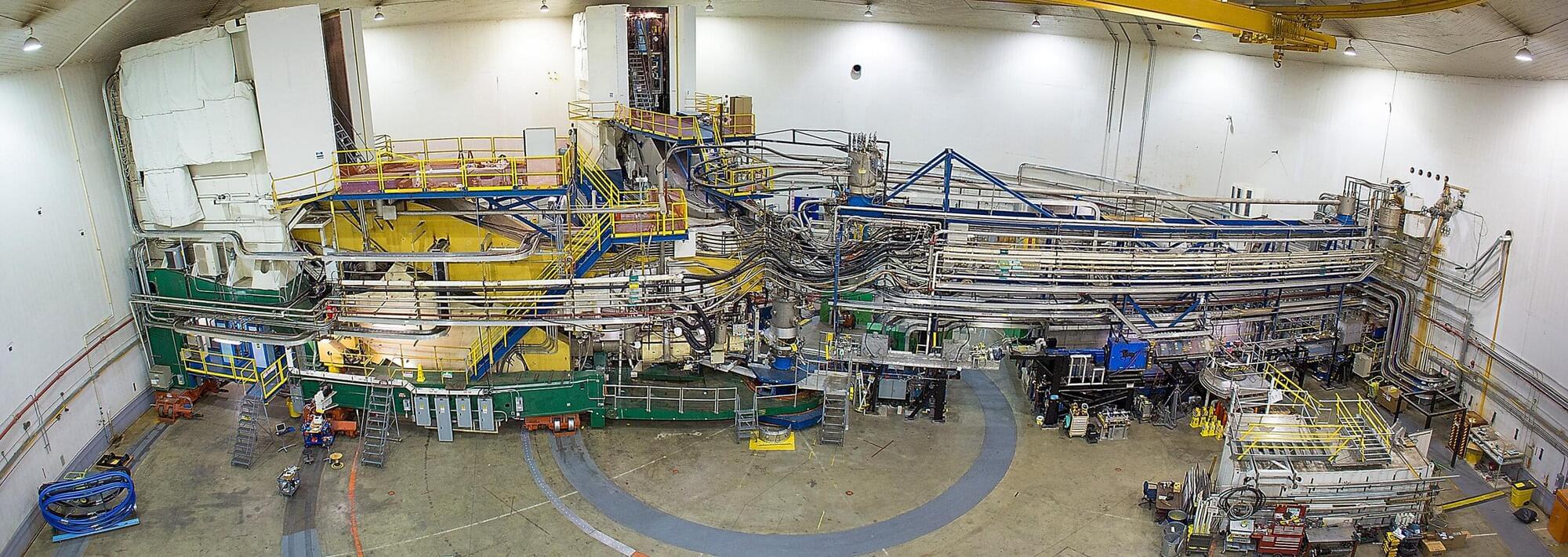
MARATHON experiment offers most precise measurement of nucleon structure yet
Nucleons, which include protons and neutrons, are the composite particles that make up atomic nuclei. While these particles have been widely studied in the past, their internal structure has not yet been fully elucidated.
These particles are known to consist of three smaller building blocks known as quarks, held together by strong nuclear force carriers called gluons. While a proton is made of two “up” quarks and one “down” quark, a neutron is made of one “up” quark and two “down” quarks.
Inside nucleons, however, one can also find many quark-antiquark pairs that continuously appear and disappear. The distribution of momentum and spin across all the different building blocks of nucleons has not yet been uncovered.