Where reality meets perspective in the choice between order and chaos
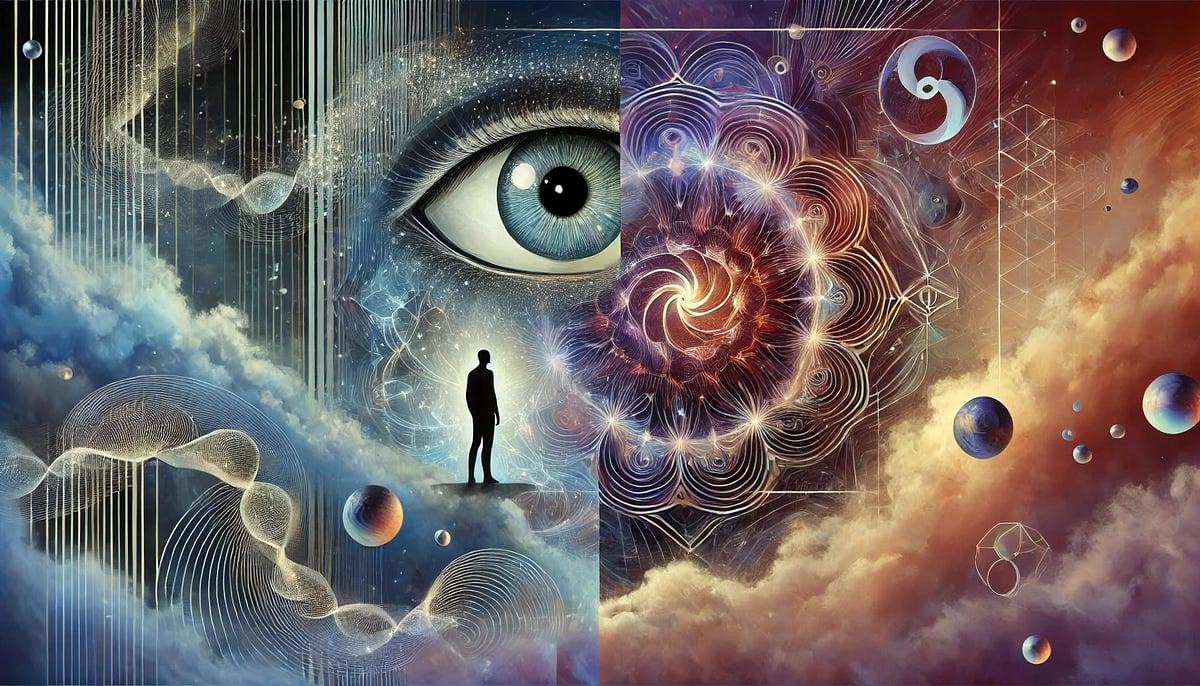
Take note of the name: ReHMGB1. A new study pinpoints this protein as being able to spread the wear and tear that comes with time as it quietly travels through the bloodstream. This adds significantly to our understanding of aging.
Short for reduced high mobility group box 1, ReHMGB1 triggers senescence in cells, permanently disabling them. It doesn’t just do this locally; it can send damaging signals throughout the body, particularly in response to injuries or disease.
“An important question in aging research is why senescent cells increase with age,” write the study authors, led by researchers from the Korea University College of Medicine.
A new study, led by researchers at Children’s Hospital of Philadelphia (CHOP), identified tiny pieces of messenger RNA that are missing in pediatric high-grade glioma tumors but not in normal brain tissues. Preclinical research indicates that these missing RNA fragments can make difficult-to-treat tumors more responsive to immunotherapy. The findings were recently published in the journal Cell Reports.
One of the biggest challenges facing cancer research is the need to find safe and effective therapies for the most aggressive types of brain tumors. Adoptive immunotherapies with CAR-T cells are promising; however, they often also target healthy cells, which share most surface proteins with cancerous cells. While this collateral damage might be tolerable in patients with certain types of blood cancer, in the brain, wiping out healthy neurons is unacceptable. This means that deep knowledge of gene expression patterns exclusive to tumor cells is critical.
A potential means of discovering new therapeutic targets for brain tumors may lie in alternative splicing, a process whereby a single gene produces multiple proteins by rearranging exons, the building blocks of messenger RNA, in different combinations. Researchers suspected that splicing in glioma cells may differ from splicing in normal brain cells, which could help devise new therapeutic interventions.
Synthetic cells are artificial constructs designed to mimic cellular functions, offering insights into fundamental biology, as well as promising impact in the fields of medicine, biotechnology, and bioengineering. In this perspective, the authors highlight major scientific hurdles, such as the integration of functional modules by ensuring compatibility across diverse synthetic subsystems, and propose strategies to advance the field.
Superconducting quantum computers dominate current development, but integrated photonics offers an alternative that uses photons instead of electrons for quantum information processing. Photonic qubits operate at room temperature rather than near absolute zero, maintain quantum properties longer, and resist environmental interference better than superconducting approaches. The technology applies established semiconductor manufacturing to build quantum circuits on silicon chips, addressing key challenges in scaling to millions of qubits, integrating components on single devices, ensuring reliable operations, and creating commercially viable systems. This approach suits applications where operational consistency takes precedence over raw computational speed.
Integrated photonics enhances quantum computing with photonic qubits, offering improved stability and scalability through established semiconductor techniques.
Quantum dots – semiconductor nanostructures that can emit single photons on demand – are considered among the most promising sources for photonic quantum computing. However, every quantum dot is slightly different and may emit a slightly different color. This means that, to produce multi-photon states we cannot use multiple quantum dots. Usually, researchers use a single quantum dot and multiplex the emission into different spatial and temporal modes, using a fast electro-optic modulator. Now here comes the technological challenge: faster electro-optic modulators are expensive and often require very customized engineering. To add to that, it may not be very efficient, which introduces unwanted losses in the system.
The international research team, led by Vikas Remesh from the Photonics Group at the Department of Experimental Physics of the University of Innsbruck and involving researchers from the University of Cambridge, Johannes Kepler University Linz, and other institutions, has now demonstrated an elegant solution that sidesteps these limitations. Their approach uses a purely optical technique called stimulated two-photon excitation to generate streams of photons in different polarization states directly from a quantum dot without requiring any active switching components. The team demonstrated their technique by generating high-quality two-photon states with excellent single-photon properties.
“The method works by first exciting the quantum dot with precisely timed laser pulses to create a biexciton state, followed by polarization-controlled stimulation pulses that deterministically trigger photon emission in the desired polarization”, explain Yusuf Karli and Iker Avila Arenas, the study’s first authors. “It was a fantastic experience for me to work in the photonics group for my master’s thesis, remembers Iker Avila Arenas, who was part of 2022–2024 cohort of the Erasmus Mundus Joint Master’s program in Photonics for Security Reliability and Safety and spent 6 months in Innsbruck.
What makes this approach particularly elegant is that we have moved the complexity from expensive, loss-inducing electronic components after the single photon emission to the optical excitation stage, and it is a significant step forward in making quantum dot sources more practical for real-world applications, notes Vikas Remesh, the study’s lead researcher. Looking ahead, the researchers envision extending the technique to generate photons with arbitrary linear polarization states using specially engineered quantum dots.
The study has immediate applications in secure quantum key distribution protocols, where multiple independent photon streams can enable simultaneous secure communication with different parties, and in multi-photon interference experiments which are very important to test even the fundamental principles of quantum mechanics, explains Gregor Weihs, head of the photonics research group in Innsbruck.
In heterotrophs, incuding animals, survival depends on the net energy gained through foraging. The expectation, then, is that natural selection results in adaptations for efficient foraging that optimize the balance of searching costs and rewards. Lévy flight foraging has been proposed as an optimal foraging solution. The hypothesis states, if no information about resource locations are available, and the locations are re-visitable, then selection will result in adaptations for Lévy flight foraging, a type of random walk. It has been argued that Levy-like foraging behaviour may simply reflect how resources are distributed, but empirical and theoretical research suggests that this behaviour is intrinsic or innate. However, this research does not address evolutionary mechanisms, and lacks ecological breadth. We extend the current theoretical framework by including evolutionary ecological contexts. We treat an organism’s random walk as a heritable trait, and explore ecological contexts such as population size, lifespan, carrying capacity, searching costs, reproductive strategies, and different distributions of food. Our evolutionary simulations overwhelmingly resulted in selection for Lévy-like foraging, regardless of the distribution of food, and evidences Lévy flight foraging as a bet-hedging strategy. Thus, here we provide some of the first evidence for the evolutionary maintenance of Lévy flight foraging.
Citation: Campeau W, Simons AM, Stevens B (2022) The evolutionary maintenance of Lévy flight foraging. PLoS Comput Biol 18: e1009490. https://doi.org/10.1371/journal.pcbi.
Editor: Marcos Gomes Eleuterio da Luz, Universidade Federal do Parana, BRAZIL.
Koonin, E., Aravind, L. Origin and evolution of eukaryotic apoptosis: the bacterial connection. Cell Death Differ 9, 394–404 (2002). https://doi.org/10.1038/sj.cdd.