Would you like fries with your nano-nuggets?
Category: nanotechnology – Page 266
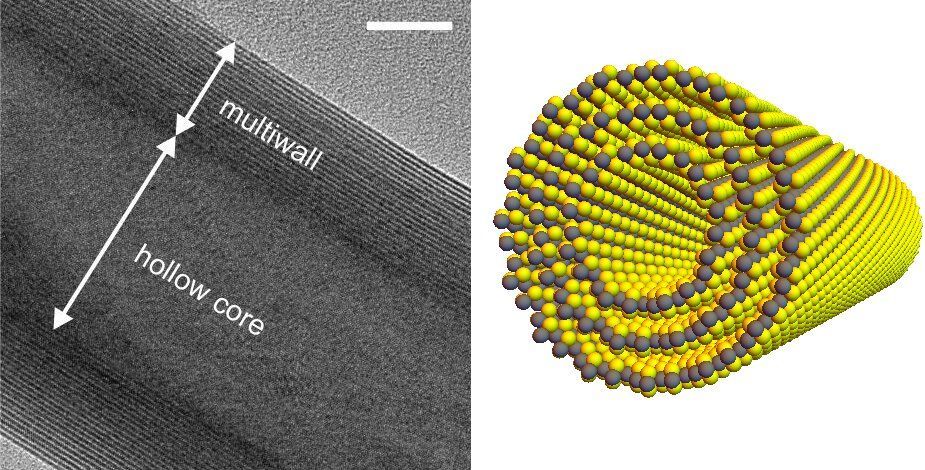
Special nanotubes could improve solar power and imaging technology
Physicists have discovered a novel kind of nanotube that generates current in the presence of light. Devices such as optical sensors and infrared imaging chips are likely applications, which could be useful in fields such as automated transport and astronomy. In future, if the effect can be magnified and the technology scaled up, it could lead to high-efficiency solar power devices.
Engineers boost output of solar desalination system
Rice University’s solar-powered approach for purifying salt water with sunlight and nanoparticles is even more efficient than its creators first believed.
Researchers in Rice’s Laboratory for Nanophotonics (LANP) this week showed they could boost the efficiency of their solar-powered desalination system by more than 50% simply by adding inexpensive plastic lenses to concentrate sunlight into “hot spots.” The results are available online in the Proceedings of the National Academy of Sciences.
“The typical way to boost performance in solar-driven systems is to add solar concentrators and bring in more light,” said Pratiksha Dongare, a graduate student in applied physics at Rice’s Brown School of Engineering and co-lead author of the paper. “The big difference here is that we’re using the same amount of light. We’ve shown it’s possible to inexpensively redistribute that power and dramatically increase the rate of purified water production.”
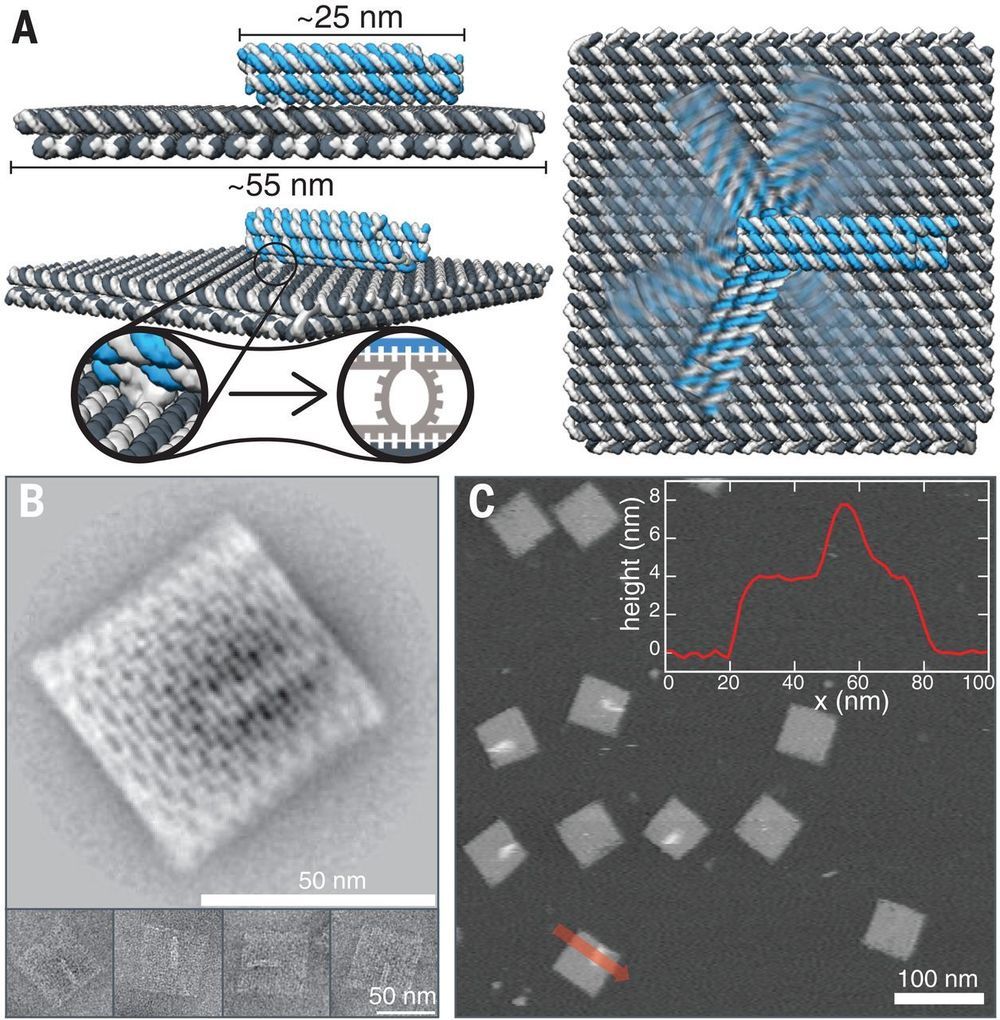
A self-assembled nanoscale robotic arm controlled by electric fields
Most nanoelectromechanical systems are formed by etching inorganic materials such as silicon. Kopperger et al. improved the precision of such machines by synthesizing a 25-nm-long arm defined by a DNA six-helix bundle connected to a 55 nm-by-55 nm DNA origami plate via flexible single-stranded scaffold crossovers (see the Perspective by Hogberg). When placed in a cross-shaped electrophoretic chamber, the arms could be driven at angular frequencies of up to 25 Hz and positioned to within 2.5 nm. The arm could be used to transport fluorophores and inorganic nanoparticles.
Science, this issue p. 296; see also p. 279
The use of dynamic, self-assembled DNA nanostructures in the context of nanorobotics requires fast and reliable actuation mechanisms. We therefore created a 55-nanometer–by–55-nanometer DNA-based molecular platform with an integrated robotic arm of length 25 nanometers, which can be extended to more than 400 nanometers and actuated with externally applied electrical fields. Precise, computer-controlled switching of the arm between arbitrary positions on the platform can be achieved within milliseconds, as demonstrated with single-pair Förster resonance energy transfer experiments and fluorescence microscopy. The arm can be used for electrically driven transport of molecules or nanoparticles over tens of nanometers, which is useful for the control of photonic and plasmonic processes. Application of piconewton forces by the robot arm is demonstrated in force-induced DNA duplex melting experiments.
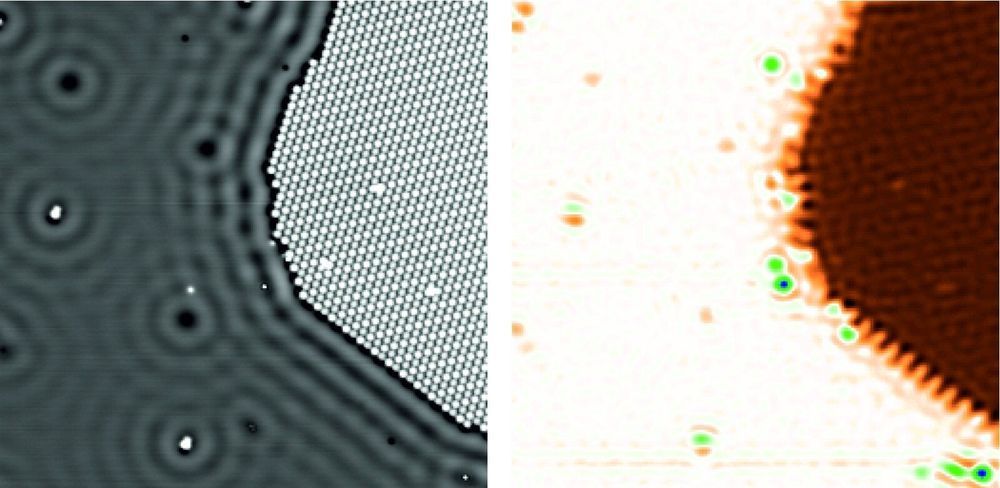
New quantum dot microscope shows electric potentials of individual atoms
A team of researchers from Jülich in cooperation with the University of Magdeburg has developed a new method to measure the electric potentials of a sample at atomic accuracy. Using conventional methods, it was virtually impossible until now to quantitatively record the electric potentials that occur in the immediate vicinity of individual molecules or atoms. The new scanning quantum dot microscopy method, which was recently presented in the journal Nature Materials by scientists from Forschungszentrum Jülich together with partners from two other institutions, could open up new opportunities for chip manufacture or the characterization of biomolecules such as DNA.
The positive atomic nuclei and negative electrons of which all matter consists produce electric potential fields that superpose and compensate each other, even over very short distances. Conventional methods do not permit quantitative measurements of these small-area fields, which are responsible for many material properties and functions on the nanoscale. Almost all established methods capable of imaging such potentials are based on the measurement of forces that are caused by electric charges. Yet these forces are difficult to distinguish from other forces that occur on the nanoscale, which prevents quantitative measurements.
Four years ago, however, scientists from Forschungszentrum Jülich discovered a method based on a completely different principle. Scanning quantum dot microscopy involves attaching a single organic molecule—the quantum dot—to the tip of an atomic force microscope. This molecule then serves as a probe. “The molecule is so small that we can attach individual electrons from the tip of the atomic force microscope to the molecule in a controlled manner,” explains Dr. Christian Wagner, head of the Controlled Mechanical Manipulation of Molecules group at Jülich’s Peter Grünberg Institute (PGI-3).
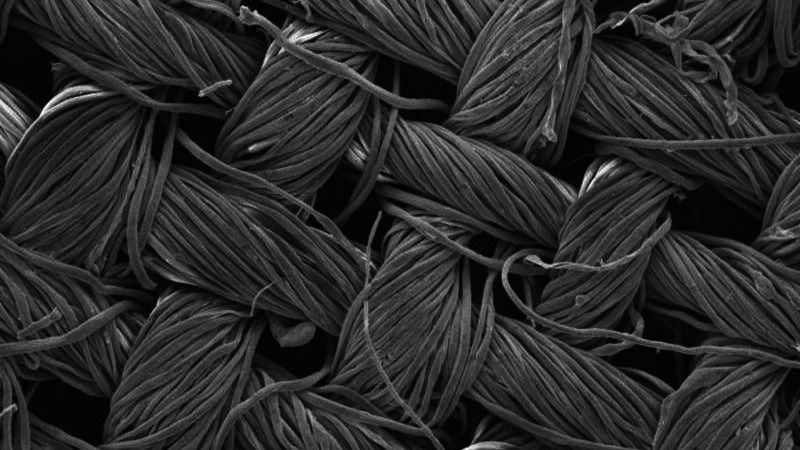
Self-cleaning Clothes Made Possible By Nano-enhanced Textile
Circa 2016
Not a big fan of laundry day? Well what if you could wash your clothes just by stepping into the sunshine? Thanks to researchers at RMIT University in Melbourne, a self-cleaning textile could make that possible in the very near future. With the help of special nanostructures grown directly into the fabric, these new textiles could degrade organic matter like dirt, dust, and sweat when exposed to a concentrated light source.
To achieve this effect, the nanostructures used by the RMIT University team are made copper and silver. These metals are great at absorbing visible light, and when they’re exposed to light from the sun or even a light bulb, the nanostructures react with increased energy that creates “hot electrons”.
Hot electrons have to expend their excess energy somehow, and in this case they do so with a rapid burst that lets the nanostructures degrade organic molecules. Once a light source is introduced, the nanostructures take less than six minutes to break down organic matter — in effect cleaning themselves completely.
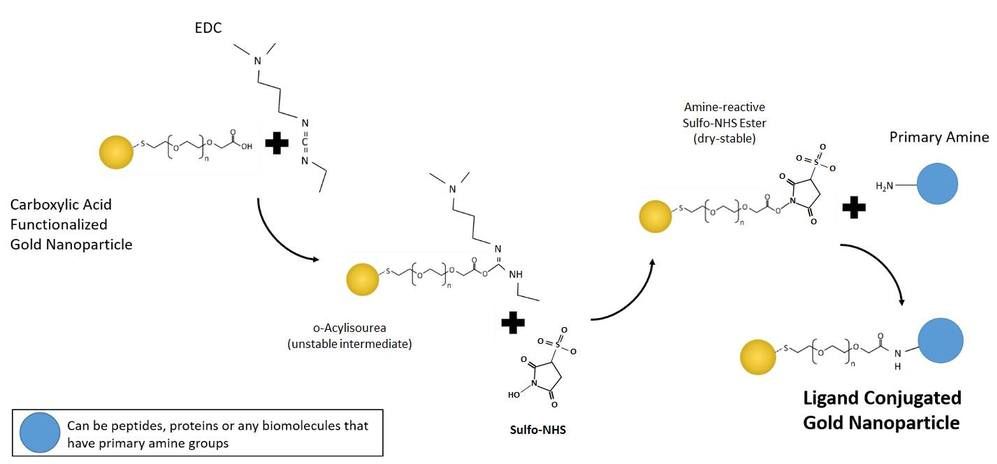
Conjugating Carboxylic Acid Functionalized Gold Nanoparticles
Conjugating Carboxylic Acid Functionalized Gold Nanoparticles, unlike other gold nanoparticles, are pre-ready for covalent conjugation. The carboxlic acid groups on the surface of the gold nanoparticles are easily reacted with primary amines via a condensation reaction which yields strong amide bonds. Usually, this is achieved by using a water-soluble carbodiimide linker such as EDC.
https://nanohybrids.net/pages/conjugating-carboxyl-functiona…oparticles
⬇️
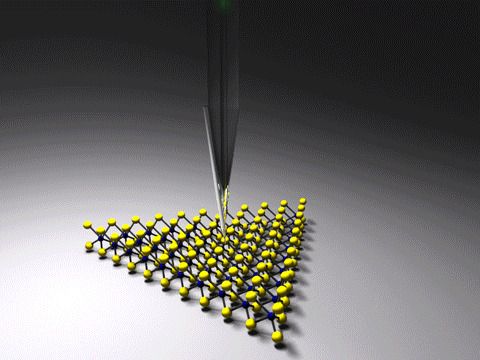
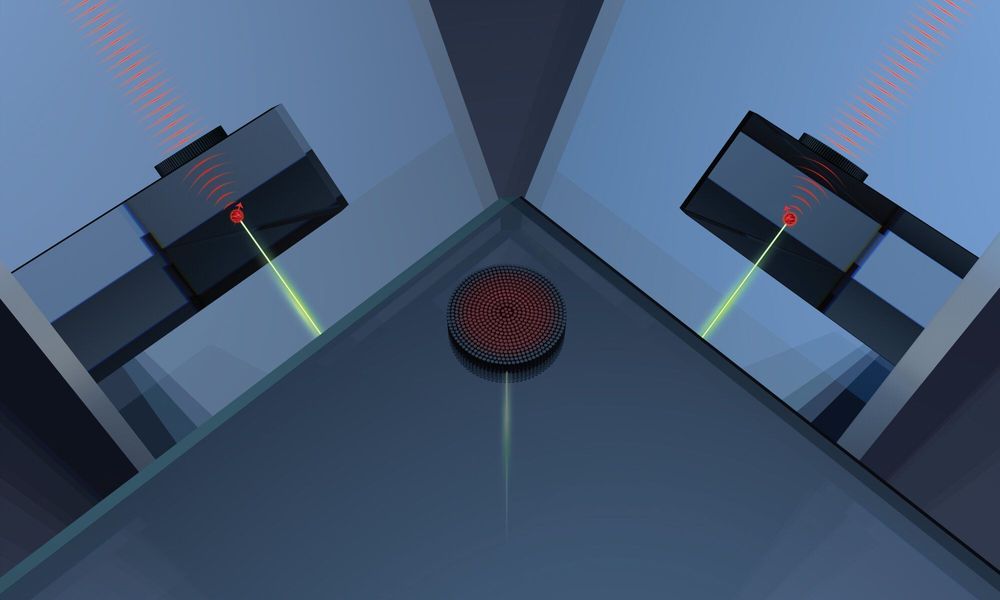
Engineers design nanostructured diamond metalens for compact quantum technologies
At the chemical level, diamonds are no more than carbon atoms aligned in a precise, three-dimensional (3D) crystal lattice. However, even a seemingly flawless diamond contains defects: spots in that lattice where a carbon atom is missing or has been replaced by something else. Some of these defects are highly desirable; they trap individual electrons that can absorb or emit light, causing the various colors found in diamond gemstones and, more importantly, creating a platform for diverse quantum technologies for advanced computing, secure communication and precision sensing.
Quantum technologies are based on units of quantum information known as “qubits.” The spin of electrons are prime candidates to serve as qubits; unlike binary computing systems where data takes the form of only 0s or 1s, electron spin can represent information as 0, 1, or both simultaneously in a quantum superposition. Qubits from diamonds are of particular interest to quantum scientists because their quantum-mechanical properties, including superposition, exist at room temperature, unlike many other potential quantum resources.
The practical challenge of collecting information from a single atom deep inside a crystal is a daunting one, however. Penn Engineers addressed this problem in a recent study in which they devised a way to pattern the surface of a diamond that makes it easier to collect light from the defects inside. Called a metalens, this surface structure contains nanoscale features that bend and focus the light emitted by the defects, despite being effectively flat.
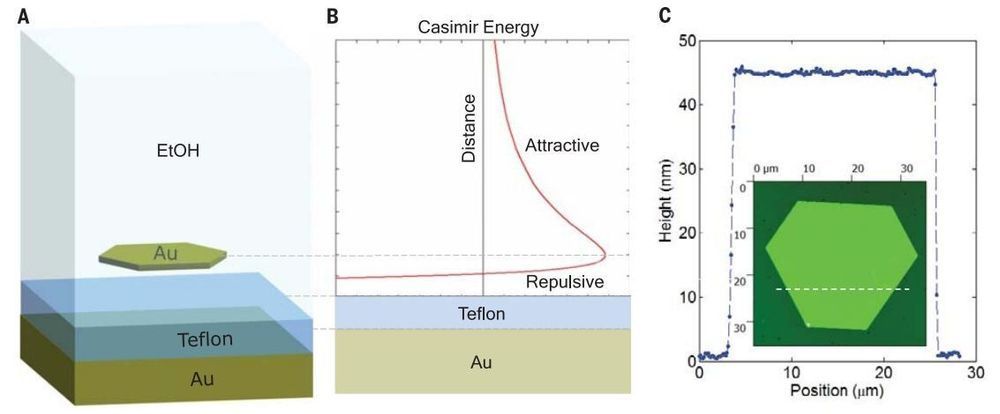
Researchers find a way to make Casimir effect attract or repulse depending on gap size
A team of researchers from the University of California at Berkeley and Lawrence Berkeley National Laboratory has found a way to make the Casimir effect attract or repulse depending on the size of the gap between two objects. In their paper published in the journal Science, the group describes their technique and possible applications.
The Casimir effect, first proposed by Hendrik Casimir back in 1948, is the phenomenon in which two tiny surfaces in close proximity experience a force that pulls them closer together. Quantum fluctuations inside and outside of the gap push against the plates, but because those pushing from the outside are stronger, they create an attractive force between the two plates. The Casimir effect is more than a curiosity, because it can create problems in nanotechnology applications.
Just two years after Casimir first proposed the effect, others in the field began making predictions about ways to counter it—making it repulsive rather than attractive, for example, in the case of fluids and plates made of lower refractive metals. Then, in 2010, a team at MIT suggested that it should be possible to counter both attractive and repulsive effects to create a state of equilibrium between the two plates. In this new effort, the researchers report that they have done just that.